
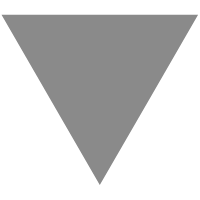
Register unplanned use of spare parts with RF
source link: https://blogs.sap.com/2022/06/09/register-unplanned-use-of-spare-parts-with-rf/
Go to the source link to view the article. You can view the picture content, updated content and better typesetting reading experience. If the link is broken, please click the button below to view the snapshot at that time.
Register unplanned use of spare parts with RF
Some time ago, a public transportation company came to us with a question about the management of unplanned spare parts for the maintenance of vehicles. Many other companies with maintenance services are struggling with this as well. It is often difficult to plan which parts you will need in advance as unplanned incidents occur too often. Whenever a request for an unplanned spare part comes in, your technician has to write this on a piece of paper and hand this over to the supervisor who will manually add this consumption into SAP EWM.
To simplify this task and to apply some checks in the background, we developed an RF application that allows a technician to easily register the unplanned use of spare parts directly in EWM. You can read how it works here.
Direct delivery order?
A direct delivery order refers to the collection of goods from the warehouse without a prior reference document in ECC or S/4HANA. A direct delivery order may originate from:
- direct sales: the customer picks up the goods directly on-site in the warehouse. No sales order is created. An internal document number gets created directly in EWM and is sent to S/4HANA where it can be used for billing.
- account assignment: the customer, either internal or external, picks up the goods directly on-site in the warehouse. No sales order is created. In contrast with the direct sales, the goods issue here happens with an account assignment (cost center or internal order). This is the part we simplified via RF.
Business configuration Set
The SAP-team can activate two business configuration (BC) sets – a predefined set of data – that will activate the correct delivery and item types in customizing to execute this process. This will help you in generating the necessary data without setting it up manually:
- /SCWM/DLV_OUTBOUND_DIRODO_1 – direct delivery without picking
- /SCWM/DLV_OUTBOUND_DIRODO_2 – direct delivery with picking
Customizing
Below are all the settings that need to be executed by the SAP-team:
Allow the correct account assignment categories and assign these categories to the warehouse. EWM > Goods Issue Process > Outbound Delivery > Define Account Assignment Category and Allow in Warehouse Number

Account Assignment Category – 1

Account Assignment Category – 2
Set up a batch job for program /SCWM/R_ACC_IMP_ERP to ensure that the cost centers and internal orders are available for use in EWM. Make sure this runs overnight to stay up-to-date every day. This batch job is no longer needed if you work with embedded EWM in S/4HANA.
Map EWM document type OPIG with the correct ERP delivery type. The document type OPIG will be activated via the BC-set. The easiest way is to take a copy from standard delivery type LO (ZLO) to be able to change the configuration in the future when needed. Do the same for the item category DLN (ZDLN).
LE > SAP EWM Integration > Outbound Processes > Direct Outbound Deliveries

Delivery Type Determination – 1

Delivery Type Determination – 2
In the screen below, specify the shipping point but leave the loading group empty. The loading group must be specified in ERP, not in EWM. Therefore, this field should be left blank.
Logistics Execution > Shipping > Basic Shipping Functions > Shipping Point and Goods Receiving Point Determination > Set Up Storage Location dependent Shipping Point Determination > Assign Shipping Points According to Storage Location

Shipping Point Determination
When you create a direct delivery order, a customizing node in EWM enables you to prefill certain data already based on the warehouse you are working in, like default ship-to party,…
Extended Warehouse Management > Master Data > Assign Warehouse Number

Warehouse Defaults
Before the operator confirms the direct delivery order, the system obviously should check how many materials are still available in the warehouse.. This is done via an easily configurable hard-coded standard availability check in ECC, APO or EWM – depending on your implementation. This prevents the technician from taking stock already reserved for other purposes or customers.
This availability check will be configured based on the entitled to dispose & the item type being used in the outbound delivery. There is the option to do a check in ERP, APO or in EWM. We choose ERP as this is the master for availability in our case.
Extended Warehouse Management > Interfaces > Availability Check > Define Configuration of Availability Check

ATP Check
Functional execution
The technician uses transaction /SCWM/SGI to create, manage and goods issue the direct delivery that will register his unplanned use of a spare part. The screenshot below shows the result.
This is the information that you need to fulfill this step:
- Product
- Quantity
- Goods movement bin
- Ship-to party (derived from the defaults of our warehouse)
- Handling Units if requested

/SCWM/SGI – Manual Direct Delivery
RF to replace paper
As our customer operates in the public transport, they regularly need to carry out maintenance work on their vehicles. They try to plan these activities and reserve the materials as far as possible.However, it sometimes happens that a technician needs a spare part that has not been reserved. He then goes to the warehouse, takes the material he needs and uses it to carry out his task.
In the past, the technician would simply write the consumption of this unplanned material on a piece of paper. Now that the company has migrated to EWM, they wanted to introduce RF scanners. This is how we set it up.
Start RF application
Scan cost centre
All users have their own cost center, which is set as a user parameter in the user profile. Once they log on to the scanner, the system knows which cost centre to use. If the user is not allocated to a cost centre, a screen will pop up to scan the cost centre.
Scan internal order
The internal order refers to an order number that is generated per maintenance centre and per division. This way, you can allocate the costs to the correct division. As the next phase is to integrate SAP PM, you can also use this field to scan the maintenance order that you are currently executing.
Scan maintenance order
In the case of our customer, the maintenance orders are still created in the previous system. To maintain the link between the direct delivery and the maintenance orders, they also scan the job order number. This is added as a z-field in the direct delivery as a reference.
Select starting point
Choose if you want to register the consumption based on the product (article number) or the location (storage bin). As a technician, you are free to choose: you often know the article numbers and the storage bins by heart.
Start Consumption based on Product or Storage Bin
Storage bin as a starting point
If you use the storage bin as a starting point, you will be requested to scan it.
Scan Storage Bin
The system will check for available stock in the storage bin and display the product number, description and available quantity (“Beschikbaar”). This is the available quantity from /SCWM/AQUA. If only one product is available, the system will immediately display this product.
Product/Qty Overview
If multiple products are available on the storage bin, the system will display a list with all possibilities. You choose the correct product by entering the row number.
Product as a starting point
If you know the article number by heart, you can enter the product number on your RF device. The system will prompt you the correct storage bin to retrieve the product. It will then again show you how many pieces are available.
Confirm consumption
Once you have chosen the correct material from the right storage bin, the system will ask for the desired quantity. Click on plus or minus to add or withdraw quantity.
The price of the product is mentioned to make you aware of the total cost. This should help prevent overconsumption of certain materials.
Enter Qty to consume
You choose OK to confirm. The system will perform an ATP check on material availability in ERP. If the material is available, a green screen will appear. In the background, a direct delivery order is created and goods are issued in EWM.
When the technician needs more materials with the same parameters (cost centre, internal order and maintenance order), he clicks on Next (“Volgende”). If no other product is needed, he clicks on Close (“Afsluiten”), which will bring them back to the RF start menu.

Successful Consumption
Error handling
If the quantity entered is bigger than the available quantity, the system will prompt an error message. It will adjust the quantity to the available quantity – the quantity between brackets.
QTY entered > available QTY

Qty requested greater than qty available
If the ATP check indicates that the quantity entered is not available , the system prompts an error message. The creation of the direct delivery will be aborted. As a result, no consumption of the material is registered, and the technician knows he’s not allowed to use this material.
Available QTY = 0

No stock available
Conclusion
The customer is very happy with this application because they are now finally able to create an overview of all the unplanned consumption of spare parts. This gives them better insights in both the quantities used and the costs related to these materials and it resulted in less stock corrections at the end of the year.
They were even able to do some seasonal predictive analysis with this overview making sure the correct materials were on time in the warehouse in the correct amounts to avoid shortages during the peaks.
Besides the functional benefits, it was a true challenge in developing the application. We had to take into account the ATP check before the commit of the document, had some additional requirements from the customer in displaying the available quantity on the screen, different screens for different technicians,… But it’s the result that matters!
Do you recognize these issues in your company or in your warehouse? Do you feel that you are losing visibility when it comes to unplanned consumption of spare parts?
Let’s talk!
Links
https://help.sap.com/docs/SAP_SUPPLY_CHAIN_MANAGEMENT/57574d15fa1d414792d74047b66c3e41/4e15e72f46485176e10000000a42189b.html
https://blogs.sap.com/2015/12/22/direct-outbound-delivery-process-in-ewm/
Recommend
About Joyk
Aggregate valuable and interesting links.
Joyk means Joy of geeK