
4
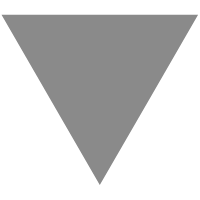
电科 | 电子器件微纳米加工技术
source link: https://blog.51cto.com/dlhjw/5285673
Go to the source link to view the article. You can view the picture content, updated content and better typesetting reading experience. If the link is broken, please click the button below to view the snapshot at that time.
电科 | 电子器件微纳米加工技术
原创电子器件微纳米加工技术
仅供参考 仅供参考 仅供参考 仅供参考 仅供参考 仅供参考 仅供参考 仅供参考 仅供参考 仅供参考
0.1 *微纳米技术 包括哪几个方面以及它们的共同点
- 三个方面:集成电路技术、微系统技术、纳米技术;
- 共同点:微纳米技术、功能结构的尺寸在微米或者纳米范围内、能带来原材料和能源的节省、导致多功能的高度集成化和生产成本的降低;
0.2 *以平面集成为基础 的 微纳米加工技术 的基本过程
- 薄膜沉积:当
要加工的微纳米结构材料不是衬底本身
,任何一种新材料都要通过薄膜沉积的方法沉积到衬底上。 - 图像成型:
微纳米尺度的结构
通过图形成像
的方法制作在平面衬底或平面衬底的薄 膜上
。(平面工艺、探针工艺、模型工艺); - 图形转移:将成像材料的图形结构转移到平面衬底上(刻蚀法、沉积法);
0.3 *平面集成加工 与 传统机械加工 的主要不同之处
- 本质区别:
平面集成加工形成的部件
或结构本身的尺寸大小
在微米或纳米范围内; - 微细结构由
曝光成像
的方法形成,而不是加工工具与材料的直接相互作用。限制加工结构尺寸的不是加工工具本身的尺寸,而是成像系统的分辨率
; - 平面工艺一般只能形成
二维平面结构
或准三维结构
。三维器件只能通过二维结构叠加而成; - 传统加工是先加工各个部件,然后装配成系统;而平面集成加工则是系统中的
每个部件以及它们之间的关系都是在平面加工过程中形成
。微纳加工重点考虑的是层与层之间的关系
,而不是各个部件之间的关系;
0.4 英文缩写
- 显微镜:扫描探针显微镜-
SPM
、扫描隧道显微镜-STM
、原子力显微镜-AFM
、近场扫描光学显微镜-NSOM、扫描电子显微镜-SEM
、透射电子显微镜-TEM
; - 光刻胶/抗蚀剂材料:光酸酵母-
PAG
(一种化学放大光刻胶)、聚甲基丙烯酸甲酯-PMMA
(高分辨率电子束正型抗蚀剂)、一种基于二氧化硅的无机类化合物-HSQ
(无机型抗蚀剂)、聚二甲基戊二酰亚胺-PMGI
(抗蚀剂); - 压印材料:氢硅酸盐-
HSQ
(纳米压印材料)、聚二甲基硅氧烷-PDMS
(印章材料); - 其他材料:液态金属离子源-
LMIS
(聚焦离子束中的离子源)、铅锆钛化合物-PZT
(压电材料)、酸性腐蚀与醋酸混合-HNA
(腐蚀液)、两层单晶硅中间夹一层二氧化硅的一种硅片-SOI
(缺口效应)、碳纳米管-CNT
、自组装单分子层-SAM
、嵌段共聚物-BCP
、聚苯乙烯-PS
; - 技术:后烘-
PEB
、多层抗蚀剂表面成像技术-TSI
、面向制造的设计-DFM
、反应离子刻蚀-RIE
(去除镓离子污染的最简单方法)、基于紫外固化作用的纳米压印技术-UV
、曝光-压印混合光刻-CNP
、喷墨闪光压印技术-J-FIL
、利用毛细管作用实现微铸模复制-MIMIC
、卷对卷连续输送-R2R
、金属辅助化学腐蚀-MACE
; - 图形转移技术:连续喷墨-
CCD
、断续喷墨-DOD
、静电纺丝喷墨打印技术-E-jet
、掠角沉积法-GLAD
; - 薄膜沉积技术:物理气相沉积-
PVD
、化学气相沉积-CVD
、原子层沉积-ALD
、分子束外延-MBE
; - 刻蚀技术:电感耦合等离子体刻蚀-
ICP
、电火花加工-EDM
(其他物理刻蚀); - 间接纳米加工技术:横向抽减法-
FIB
、吸收调制光学曝光-AMOL
(超级分辨率法); - 现象效应:表面等离子极化现象-
SPP
、延迟效应-PED
; - 参数:图形分辨率-
DNP
、与刻蚀深宽比相关的负载效应-ARDE
(负载效应); - 其他:
- 由厚胶曝光后形成深结构,然后电铸,使之转化为金属深结构,得到微系统器件所需要的功能结构 -
LIGA
技术;
- 由厚胶曝光后形成深结构,然后电铸,使之转化为金属深结构,得到微系统器件所需要的功能结构 -
1. 光学曝光技术
1.1 *光学曝光 分辨率增强技术 有哪些
- 根据公式:R=K1NAλR=\frac{K_1}{N_A}λR=NAK1λ 可知:
- 短波长曝光技术:以准分子激光器作为光源;
- 利用浸没式曝光增大数值孔径 NA;
- 减小 K1 或 增强光学成像分辨率:
- 离轴照明技术:遮住中心轴部分的照明光,只让轴外部分的照明光进入透镜;
- 空间滤波技术:在
频域空间
调制掩模成像的光强和相位,以改善图形的 分辨率 和 焦深; - 移相掩模技术:通过
对光波相位的调制
来改善成像 对比度 和 焦深; - 光学临近效应校正技术:有意
改变掩模设计的形状和尺寸
来补偿图形局部曝光过强或过弱; - 面向制造的掩模设计技术:通过改变
调整电路设计
以适应具体的制造工艺; - 光刻胶及其工艺技术:可以使 k1 因子的降低(K1因子指:包含所有透镜光学之外的对成像分辨率产生影响的因素);
1.2 *光学曝光的基本工艺流程
- 硅片表面处理:即:
去污+干燥
。常规化学清洗;烘烤使其绝对干燥以保证光刻胶附着性好;涂化学增附剂 HMDS,确保光刻胶在后续刻蚀中不脱落。 - 涂胶:硅片涂胶又称甩胶。把光刻胶滴在硅片的中央,然后通过
高速旋转
使胶均匀地甩在整个硅片表面。胶的厚度可以通过旋转速度来控制。还有喷涂(喷雾器)方法。 - 前烘:目的是蒸发掉胶中的有机溶剂成分,使硅片表面的
胶固化
。可在热板或烘箱中进行。每一种胶都有其特定的前烘温度和时间。 - 曝光:首先要进行对准(非第一次曝光),然后选定曝光剂量,在曝光机上进行曝光。
- 后烘:即:
消除驻波
。光线照射到光刻胶与硅片的界面上会产生部分反射,反射光与入射光叠加会形成驻波。后烘会消除这种效应; - 显影:有浸没法、喷淋法和搅拌法。浸没法指将硅片浸入
显影液
池中一段时间,然后取出并清洗掉残留的显影液。喷淋法是将显影液喷淋到高速旋转的硅片表面,清洗和干燥也是在硅片旋转过程中完成的。喷淋法和搅拌法需要专门设备。 - 清除残胶:显影后会在硅片表面残留一层非常薄的
胶质层
。可以把显影后的硅片放在等离子体刻蚀机进行短时间刻蚀。注意,去残胶的过程会使胶层厚度减小和造成曝光图形精度的变化。 - 坚膜:通过加温烘烤使胶膜更牢固地黏附在硅片表面,
增加胶层的抗刻蚀能力
。注意,坚膜会增加去胶的难度。 - 图形转移:通过物理或化学方法把掩模设计图形转移到
硅片表面
。 - 去胶:过湿法或干法
去除光刻胶
。湿法是利用酸碱类溶液或有机溶剂腐蚀,丙酮可以溶解清除绝大多数光刻胶。干法是利用氧气等离子体刻蚀去胶。
1.3 #正性光刻胶、负性光刻胶
- 正性光刻胶:光刻胶是指一大类具有
光敏化学作用的高分子聚合物
材料,就光敏化学反应而言,聚合物的长链分子因光照而截断成短链小分子
的为正型光刻胶。采用“暗场”掩模,即掩模的大部分区域是不透光的;(目前大规模使用,对比度高、显影液水溶性、高抗刻蚀比、热稳定性好) - 负性光刻胶:光刻胶是指一大类具有
光敏化学作用的高分子聚合物
材料,就光敏化学反应而言,聚合物的短链分子因光照而交联成长链分子
的为负型光刻胶。采用“亮场”掩模,即掩模的大部分区域是透光的;(与硅片附着好、灵敏度高、成本低、显影液有机、受氧气影响遗留残胶现象普遍、显影后膨胀)
1.4 曝光方式的分类、特点及原理
- 接触式曝光:掩模与光刻胶表面完全接触;(高分辨率,机械接触)
- 邻近式曝光:掩模和光刻胶表面保持几微米到几十微米的间距;(避免接触,衍射效应影响分辨率)
- 投影式曝光:通过光学成像的方法将掩模图形投影到衬底表面,原理是:杨氏单缝衍射理论;
1.5 光刻胶的一般特性
- 概念:一大类具有光敏化学作用的高分子聚合物材料;
- 灵敏度(衡量曝光速度)、对比度(影响胶的分辨能力)、抗刻蚀比(刻蚀衬底材料的速率与刻蚀
光刻胶的速率之比)、分辨能力(综合条件,受曝光系统的分辨率、光刻胶、显影条件与前后烘温度影响)、曝光宽容度、工艺宽容度、热流动性、膨胀效应、黏度、保质期;
2. 电子束曝光技术
2.1 *邻近效应的主要表现形式、如何矫正
- 主要表现:两方面:
图形之间
、图形之中
; - 矫正:
剂量校正
:由于电子散射,在同一曝光剂量下曝光图形的能量分布是不均匀的,为了得到均匀一致的能量分布,需要人为地改变曝光剂量的分布;(最普遍、效果好),其中有分:自洽技术—物理校正
:比较精确,但对大规模集成电路设计,求解复杂,计算量大;几何图形分割法—几何校正
:计算得到的曝光剂量分布比较粗糙,但计算速度快;
图形尺寸补偿
:通过改变图形尺寸来补偿因电子散射而造成的曝光图形畸变;(校正
动态范围小)背景曝光补偿
:电子散射的结果总是使图形密集的地方能量高,图形稀疏的地方能量低;如果将所有没有图形的地方再加以曝光,则原来图形稀疏处现在变成图形密集处,原来图形密集处因为空白区域小而变成图形稀疏处。两次曝光的能量叠加正好使所有各处的能量分布均衡。称为 GHOST 方法;(简单,但只有在光栅扫描式曝光系统才是实用的)
- 减少邻近效应:
- 提高电子束能量(100keV)、减小电子束抗蚀剂厚度(减少电子前向散射);
2.2 *实现更高的 分辨率 需要考虑哪些因素
高电子能量,孔速扫灵层,优密稳;
- 高电子能量:高压下电子前向散射范围小,背散射电子分布广,局部背散射电子效应低,有利于减小电子束曝光的邻近效应;高能电子束色差和空间电荷效应低,有利于获得更小的电子束斑;高能电子束有利于曝光厚抗刻蚀剂层,形成高深宽比的图形结构。高档次的电子束曝光系统一般工作在 100 kV 的加速电压。
- 小限制膜孔:减小束张角,进而减小球差。
- 低速流:减小空间电荷效应,减小束斑,但会增加曝光时间。
- 小扫描场:减小偏转像差。
- 低灵敏度抗蚀剂(如PMMA和HSQ):分辨率小于20 nm。
- 薄抗蚀剂层:减小电子束前向散射影响,降低邻近效应。
- 优化抗蚀剂工艺:改变显影工艺。
- 低图形密度:减小邻近效应。
- 稳定的工作环境:包括低振动、低电磁干扰、稳定的环境温度等。
2.3 #前向散射、电子束背散射、快二次电子、邻近效应
- 前向散射:散射使
单点入射的电子束在抗蚀剂内扩散成很大范围
。由于电子在散射沿途将能量留在抗蚀剂内,因此电子能量在抗蚀剂中的横向分布
总是大于电子束曝光的图形,这相当于入射电子束在抗蚀剂中被展宽。造成电子束展宽的散射称为前向散射; - 电子束背散射:由于抗蚀剂与硅为两种不同材料。电子在材料界面将会形成反射。
在界面反射的电子会重新进入抗蚀剂
,对抗蚀剂曝光。这部分电子称为背散射电子; - 快二次电子:入射电子在抗蚀剂中
损失的能量会激发形成低能量二次电子
,其中有一小部分二次电子可以获得 1000eV 以上的能量。这些快二次电子可以做近距离散射扩散,造成能量分布的进一步展宽;(可能是限制电子束曝光极限分辨率的主要原因) - 邻近效应:
- 电子邻近效应:如果相邻两个曝光图形靠得非常近,由
电子散射形成的曝光能量分布将延伸到相邻的图形区域
,使曝光图形发生畸变;即使在同一图形内,散射也会使图形边缘处的能量低于中间部分的能量; - 光学邻近效应:投影式曝光光学从本质上是
衍射光学
,衍射成像会在光波传输工程中丢失部分高频能量,使图像清晰度降低。反映在掩模成像上是方角的掩模图形变成圆角,或者线端变短
,称为光学邻近效应;
- 电子邻近效应:如果相邻两个曝光图形靠得非常近,由
2.4 SEM(扫描电镜) 与 电子束曝光 的异同点及改造条件
- 相同点:扫描电镜与电子束曝光机的电子光学系统在本质上是相同的;
- 区别:扫描电镜没有图形发生器,没有激光控制的工作台,没有电子束快门;
- 改装问题:
- 扫描电镜一般不按照电子快门;
- 扫描电镜以光栅扫描方式工作,扫描电镜改装的电子束曝光要以矢量扫描方式工作,因此扫描电镜的扫描线圈不完全适应;
- 扫描电镜的工作台一般是手动的。即使有步进电动机控制,其精度也不会好于1μ吗;该问
题可以加激光控制台解决,但价格很贵; - 扫描电镜改装的电子束曝光机不适合大面积、快速曝光,但作为科学研究是可以的
2.5 低能电子束曝光 的特点
- 低能电子束曝光效率高,表现在:
- 低能电子束在抗蚀剂层和衬底材料中的穿透深度很小;
- 抗蚀剂聚合物分子的断链或交链都是在 100keV 电子能量以下发生;
- 几乎没有背散射电子返回抗蚀剂层,大大减轻了由背散射电子造成的邻近效应;
3. 聚焦离子束加工技术
3.1 *离子在 固体材料 中能量损失的原因
- 有两方面:
- 原子核损失,即离子与固体材料中原子的原子核碰撞将部分能量传递给原子,使原子或移位或完全脱离固体材料表面,这一现象称为溅射;
- 电子损失,即将能量传递给原子核周围的电子,使这些电子或被激发产生二次电子发射,或剥离固体原子核周围的部分电子,使原子电离成离子,产生二次离子发射;
3.2 *离子在固体材料散射 与 电子在固体材料散射 的异同点
- 相同点:
- 作为带电粒子,离子与电子一样在固体材料中会
发生一系列散射
,在散射过程中不断失去所携带的能量最后停留在固体材料中
; - 电子散射和离子散射过程都可以用
蒙特卡洛方法
模拟;
- 作为带电粒子,离子与电子一样在固体材料中会
- 不同点:
电子
:电子与固体材料中的原子核碰撞是弹性碰撞,碰撞后电子不损失能量,因为电子的质量远小于原子。能量传递效率低、不产生污染离子
:离子的质量与原子核相当,所以离子与固体材料中的原子核碰撞为非弹性碰撞,有能量损失。离子散射灵敏高(但曝光图形边缘的粗糙度较大)、几乎没有邻近效应、离子穿透深度较浅、几乎没有背散射效应、有离子注入污染问题;
3.3 *列举 聚焦离子束加工技术 的应用方面
- 审查与修改集成电路芯片:某一处的连线断开,改变电路连线走向,排错;
- 修复光刻掩模缺陷:可能会有镓离子污染问题;
- 制作透射电子显微镜样品:制作 TEM 样品。利用聚焦离子束从前后两个方向溅射,最后在中间留下一个薄的区域作为 TEM 观察的样品;
- 多用途微切割工具:相当于在高倍显微镜下操作的微加工台,
可用于在任何部位溅射剥 离或沉积材料
;
3.4 #沟道效应、负载效应、微沟槽效应、缺口效应、离子损伤效应(7.2)
- 沟道效应:如果衬底材料是
晶体
,在低指数晶向
,即原子排列稀疏的方向,离子有可能“长驱直入”,穿透深度
可能是非晶材料的数倍。这一现象称为“沟道效应”;
以下四种为:反应离子深刻蚀中存在的问题
- 负载效应:
局部刻蚀气体的消耗
大于供给引起的刻蚀速率下降或分布不均匀
的效应;(分三种:宏观负载效应、微观负载效应、与刻蚀深宽比相关的负载效应); - 微沟槽效应:深刻蚀过程中
边角的刻蚀深度
大于中心部分刻蚀深度
的一种现象。(刻蚀深度越深,微沟槽效应越明显); - 缺口效应:刻蚀 SOI 硅片时,刻蚀速率快的图形在刻蚀到
二氧化硅
隔离层后并没有完全停止,而是继续沿二氧化硅隔离层表面横向方向
刻蚀;(SOI 硅片由 两层单晶硅 中间夹 一层二氧化硅 形成) - 离子损伤效应:在反应离子刻蚀中总是有一部分离子在阴极电场加速下轰击刻蚀表面。离子轰击一方面形成
溅射刻蚀作用
,另一方面也会对刻蚀表面
在载流子分布
以晶格结构
造成损伤。(最有效的降低离子损伤的方法是降低离子能量
);
3.5 离子源的类型及特点
- 按工作原理分:
- 电子轰击型离子源:通过热阴极发射的电子,加速后轰击离子源室内的气体分子,使气体分子电离。这类离子源多用于质谱分析仪器。特点是束流不高,但能量分散小。
- 气体放电型离子源:由气体等离子体放电产生离子。如辉光放电、弧光发电和火花放电离子源。这类离子源的特点是产生离子束流大,因此广泛应用于核物理研究,如高能加速器的离子源和离子注入的离子源。
- 场致电离型离子源:它是利用针尖电极附近强电场使吸附在针尖表面的气体原子电离。这类离子源主要用于场致离子显微镜,研究针尖表面材料的原子结构。主要:液态金属离子源(空间发射角大利用率低、离子能散大色差大、用的最广泛)、气态场电离离子源(极小的分散角,大幅度下降聚焦系统的球差和色差,分辨率得到提升(0.25nm),效率低)
3.6 LMIS(液态金属离子源) 稳定发射必须满足三个条件
- 发射表面具有一定形状,从而形成一定的表面电场;
- 表面电场足以维持一定的发射电流与一定的液态金属流速;
- 表面流速足以维持与发射电流相应的物质流量损失,从而保持发射表面具有一定形状;
4. 扫描探针加工技术
4.1 *相比于 STM,AFM 作为局部氧化加工更适合的原因
- 局部氧化加工:硅表面在空气中会自然形成几个原子层厚的二氧化硅层,经过氢钝化在探针高电场的作用下,空气中的水分子被电离后会使针尖附近的硅表面氧化。(可作为后续刻蚀的掩模)
- 好处:有两个优点:
- AFM 的
偏压独立
于探针高度的反馈控制系统(因为 AFM 的反馈控制是由原子力决定的,而不是隧道电流); 氧化层高度
可以直接
被测量(STM 需要通过隧道电流间接测量);- *AFM
敲击模式
更适合局部氧化加工操作(敲击模式可以避免因探针扫描引起的切向力作用,同时可以克服样品表面水分子膜对针尖的黏附力);
- AFM 的
4.2 *扫描探针加工中,与 STM 相比,AFM 有哪些优势
- 工作环境:STM 依赖于隧道电子发射成像,通常需要 STM 工作在真空环境下。而 AFM 可以工作在大气环境下,甚至可以工作在液体环境中。
- 样品材料:STM 需要针尖和样品均为导体,以保证隧道电子流通。而 AFM 可以在任何材料表面成像。
- 兼容性:当 AFM 的探针和样品是导体材料时,外加偏置电压就使 AFM 变成了一个 STM。这时,AFM 具有 STM 的所有功能。
- 灵活性与应用性:AFM 比 STM 更灵活。应用更广泛。
4.3 #增材式加工技术、减材式加工技术
- 增材式加工技术:通过扫描探针将原来的材料或新材料
沉积
到样品的表面;(有:扫描探针场致沉积、蘸笔纳米光刻) - 减材式加工技术:通过扫描探针将衬底材料
抽减剥离
,形成所需要的加工图形结构;(有:电化学刻蚀加工、场致分解加工、热力压痕法加工、机械划痕法加工、氢原子掩模加工)
4.4 STM 曝光的分辨率远低于 STM 成像的分辨率的原因
- 由于总是要有一层一定厚度的抗蚀剂将STM探针与衬底材料分开,所加电压必须足够高以便电子能够穿透这层抗蚀剂,所以STM曝光的电子束总是大于作为阴极的探针直径。因此,STM曝光的分辨率永远低于STM成像的分辨率;
4.5 影响局部氧化的因素
- 施加的探针偏压、探针扫描速度(每点逗留时间)、环境空气的湿度;
4.6 高产出率 扫描探针加工 的方法
- AFM探针工作在恒定高度模式;
- 集成式压电驱动系统取代压电陶瓷管,因为集成式压电驱动系统的响应频率相对较高;
- 利用计算机硬盘磁头工作的原理,将近场光学探针做成磁头形式,被曝光的衬底是高速旋转的磁盘;
- 多探针平行加工方法
5. 复制技术
5.1 *热压纳米压印 对 压印聚合物 的要求
低玻温、粘收,好抗;
- 较低的 玻璃化转变温度:降低印模温度;
- 较低的 粘塑性:保证聚合物材料的流动性和对印模空腔的充分填充;
- 较小的 收缩性:保证冷却后的压印结构不变形;
- 较好的 抗刻蚀性:保证压印图形能够通过等离子体刻蚀完整地转移到衬底材料上;
5.2 *怎样的 脱模 会对 图形 造成损害
- 以下三种:
- 压印材料粘附在印模上;
- 印模图形侧壁表面粗糙:(可能造成)印模脱出时在 印模 与 压印图形 之间形成较大摩擦力;
- 印模浮雕结构的侧壁坡度不合理:(可能造成)拔出 印模 时连带将 压印材料 拔出;
5.3 *解决 压印材料 粘附性问题 的方法(解决5.2的问题)
- 三种:
- 选择 表面能较低 的材料作为印模材料:如:金刚石;
- 将 特殊的印模释放剂或脱模剂 与 压印材料 混合:减少印模与压印材料之间的粘附性;
- 在 印模表面 涂 脱模剂或其他抗黏材料:需要注意的是
印模浮雕结构
的边壁坡度问题
;
5.4 *实现 大面积压印 的一般方式
- 平压:难点在于
控制压力的均匀分布
以及防止局部残留气泡
; - 滚压:优势明显;
5.5 *大面积连续压印 的技术难点
- 压印模板的制备:微米以下图形尺寸的模板一般需要用
电子束曝光技术
制备。微米以上图形尺寸的模板一般用光学曝光方法
制备。(可以用步进邻近式光学曝光的方法来进行模辊的制备); - 如何均匀涂胶:即控制涂胶厚度与均匀性;
- 动态对准问题:当大面积连续压印需要与基础材料上原有图形对准时,对准精度很难达到 50μm 以下;
---- 前面是 图像成型,后面是 图像转移 ----
6. 沉积法图形转移技术
图形转移技术主要分为两大类:沉积法图形转移 与 刻蚀法图形转移;
6.1 *电镀法的 基本步骤 及其 工艺难点
- 步骤:
- 1. 制作一层
金属导电薄膜
作为电镀的起始衬底,然后制作光刻胶或抗蚀剂掩模
; - 2. 基于带有光刻胶图形的基片,在电解液中进行
金属膜的沉积
; - 3. 将
光刻胶掩膜
去除并腐蚀清除衬底表面其余的金属膜
,便得到金属微结构图形
;
- 1. 制作一层
- 难点:
- 保证电镀层的均匀性(由于电镀沉积速率主要决定于电流的大小,电流分布的均匀性就决定了电镀层的均匀性。由于电场分布与被镀表面的几何形状有关,尖角和图形尖锐边缘处的电场较高,电流也较大,造成了电镀层厚度的不均匀);
- 保证电镀层的均匀性(由于电镀沉积速率主要决定于电流的大小,电流分布的均匀性就决定了电镀层的均匀性。由于电场分布与被镀表面的几何形状有关,尖角和图形尖锐边缘处的电场较高,电流也较大,造成了电镀层厚度的不均匀);
6.2 *简单列举常用的 沉积图形转移法
薄脱双镀,嵌模喷掠;
- 原理:以光刻胶图形为掩模或用其他掩模形式将另一种材料沉积到衬底上;
- 沉积法图形转移主要依赖于各种薄膜沉积技术,根据薄膜形成的方法不同,
沉积法 图形转移
具体可以分为:溶脱剥离法、电镀法、嵌入法;还有并不依赖于光刻胶
掩模的:镂空模板法、喷墨打印法、掠角沉积法; - 薄膜沉积技术:分以下:
物理气相沉积
:热蒸发沉积、等离子体溅射沉积;化学气相沉积
:低压型、常压型、等离子体增强型、金属有机化合物型;原子层沉积
:分子束外延
:
- 溶脱剥离法:利用
下切形状的抗蚀剂剖面
实现薄膜剥离图形转移
,(可以采用多层抗蚀剂结构
实现下切剖面); - 电镀法:当需要较厚的金属结构或高深宽比微纳米金属结构时,一般通过电镀或化学镀实现图形转移。主要应用是制作
计算机硬盘驱动器的磁头
,以及填充集成电路金属互连线的连接深孔
; - 化学镀:不需要外加电源,仅通过化学反应实现金属沉积的技术;
- 嵌入法:实现多层互联,即 打通层之间的深孔 并 填充金属导电材料;
- 模板法:有:丝网模板印刷、镂空模板印刷;
- 喷墨打印法:有:连续喷墨 CCD、断续喷墨 DOD;
- 掠角沉积法:指蒸发源与样品表面呈一定角度;
6.3 *改善 溅射沉积方向性 的方法
- 方向性问题:每一种光刻胶都有一个玻璃化转化温度(Tg),当温度大于 Tg 时光刻胶开始软化并可流动,导致光刻胶图形倒塌或变形;
- 改善:
增加电极间距
:降低放电室气压 -> 溅射靶原子的自由程增大 && 大角度发射的溅射靶原子落到样品表面的概率降低 -> 总的效果使方向性得到改善;(缺点:靶材料的利用率降低)安装准直管
:只允许垂直或接近垂直飞行的溅射靶原子到达样品表面;(缺点:长时间使用会导致侧壁沉积层变厚)
6.4 *为什么 溅射的合金 组分均匀
溅射沉积
的合金薄膜
能大致保持靶材料
的合金组分。尽管不同合金组分的溅射产额不同,但是因为溅射只发生在靶材料表面
,高溅射产额组分
虽然溅射得快,但是消耗得也快
。只有将表层材料全部溅射完毕后,才能开始新一层的溅射。因此,最后形成的薄膜组分基本保持了原来靶材料的成分比例。- 合金材料中各种不同组分的蒸气压可能不同,在热蒸发沉积过程中,在某一温度下一种组分可能有很高的蒸发速率,而另一种组分的蒸发速率很低,最后成膜的合金组分可能完全不同于靶材料的合金组分;
7. 刻蚀法图形转移技术
刻蚀法图形转移:以光刻胶图形为掩模将衬底或衬底上的薄膜刻蚀清除;
7.1 *反应等离子体刻蚀中,四种同时发生的过程,请画图表示。同时,请列举对刻蚀结果有决定性影响的参数或实验条件
- 四个过程:物理溅射、离子反应、产生自由基、自由基反应;
流功温压,电极气体;
- 反应气体流速:刻蚀速率直接与反应气体供给的速率有关;
- 放电功率:电功率增加 -> 电子能量增加 -> 电离概率增加 -> 反应气体离子产生的速率增加 -> 刻蚀速率增加;
- 反应室气压:低压 -> 气体分子密度降低 -> 电子自由程增加 -> 电子在每两次碰撞之间的加速能量增加 -> 电离概率增加;
- 样品材料表面温度:适当高温 促进化学反应过程,利于挥发性产物离开刻蚀表面;
- 电极材料:被刻蚀样品放置在阴极表面,阳极和反应室侧壁接地。电极材料应该是化学惰性的;
- 辅助气体:在卤素气体中加入少量非卤素气体如氧气和氩气会在不同程度或不同方面改进刻蚀效果;
7.2 *随着刻蚀深度增加,ICP 刻蚀 (电感耦合等离子体)的 负面效应 及其特点
- 负载效应:
局部刻蚀气体的消耗
大于供给引起的刻蚀速率下降或分布不均匀
的效应;(分三种:宏观负载效应、微观负载效应、与刻蚀深宽比相关的负载效应); - 微沟槽效应:深刻蚀过程中
边角的刻蚀深度
大于中心部分刻蚀深度
的一种现象。(刻蚀深度越深,微沟槽效应越明显); - 缺口效应:刻蚀 SOI 硅片时,刻蚀速率快的图形在刻蚀到
二氧化硅
隔离层后并没有完全停止,而是继续沿二氧化硅隔离层表面横向方向
刻蚀;(SOI 硅片由 两层单晶硅 中间夹 一层二氧化硅 形成) - 离子损伤效应:在反应离子刻蚀中总是有一部分离子在阴极电场加速下轰击刻蚀表面。离子轰击一方面形成
溅射刻蚀作用
,另一方面也会对刻蚀表面
在载流子分布
以晶格结构
造成损伤。(最有效的降低离子损伤的方法是降低离子能量
);
8. 间接纳米加工技术
8.1 *常见的间接加工技术
侧垂双横,超纳
- 侧壁沉积法:通过
向侧壁沉积薄膜材料
的方法制作窄细线条结构
;(需要满足两个条件:支撑结构侧壁足够垂直、去除支撑结构时对薄膜材料无影响) - 垂直抽减法:基于
侧壁沉积间接加工相反的过程
实现纳米尺度结构的间接加工;(关键要求是支撑材料与沉积材料的刻蚀化学不兼容); - 横向抽减法:将一个宽图形
从两侧横向逐渐抽减
使之最后变成窄图形;(以获得窄细的线条结构) - 横向添加法:从一个宽的间隙开始,不断
从两端横向添加材料
,使宽的间隙变窄;(以获得窄细的间隙结构) - 纳米球阵列法:利用自组装技术在衬底表面形成排列规则的聚苯乙烯纳米小球阵列。尺寸均一的小球在衬底材料表面紧密堆积,会形成规则的间隙点阵。用热蒸发等沉积方法沉积金属薄膜时,蒸发材料会沉积在间隙处(过程包括
纳米球自组装
、蒸发镀膜
、去除纳米球掩模层
等步骤); - 超级分辨率法:利用
光学曝光的光强分布
或电子束曝光的电子束流密度分布
特性得到比普通曝光较高的分辨率的方法;
8.2 #间接纳米加工技术
- 间接纳米加工技术:指非直接光刻技术,
图形结构
的分辨率不决定于某种光刻方法
的分辨率,能够绕过现有设备加工能力极限
的方法。没有特定的规则,也不需要遵循某一原理。
9. 自组装纳米加工技术
前面是传统加工技术(涉及某种方式的光刻制作图形与图形转移技术,自上而下)。
这里是分子水平的自组装技术(最终发展),自下而上;
9.1 *自组装技术 的优势及基本特征
- 优势:两方面:
组装分子为分子尺度
,远远小于目前传统纳米加工所能实现的结构尺寸;低成本优势
,原理上,分子自组装过程是自动的、自发的,不需要昂贵的加工设备;
- 特性:有四个:
- 由个体集合形成整体组织或系统的过程是
自发的
、自动的; - 个体之间的结合是
非共价键力
的结合(晶体生长除外); - 组成整体组织或系统的个体必须能够
自由运动或迁移
; - 自组装形成的整体组织或系统是个体相互作用的
热力学平衡或能量平衡
的结果,在平衡条件下,个体之间保持等距离
和长程有序周期分布
,而不是随机聚集;
- 由个体集合形成整体组织或系统的过程是
9.2 #自组装过程
- 自组装过程:自组装是一个非常广义的概念。任何一种由独立个体自发地(无人为干涉)形成一个组织或系统的过程都可以称之为自组装过程。自组装可以是微观的、介观的或宏观的。
10. 简单记
序号 | 问题 | 简记 | 说明 |
---|---|---|---|
1 | 光学曝光分辨率增强技术 | 离空移邻制光 |
离轴照明技术、空间滤波技术、移相掩模技术、光学临近效应校正技术、面向制造的掩模设计技术、光刻胶及其工艺技术 |
2 | 邻近效应矫正 | 剂尺曝,高束能,小抗厚 |
剂量校正、图形尺寸补偿、背景曝光补偿、高电子束能量、减小电子束抗蚀剂厚度 |
3 | 电子束曝光实现更高的分辨率 | 高电子能量,孔速扫灵层,优密稳 |
高电子能量、小限制膜孔、低速流、小扫描场、低灵敏度抗蚀剂、薄抗蚀剂层、优化抗蚀剂工艺、低图形密度、稳定的工作环境 |
4 | 聚焦离子束加工技术的应用 | 审集修光制透,微切割 |
审查与修改集成电路芯片、 修复光刻掩模缺陷、制作透射电子显微镜样品、多用途微切割工具 |
5 | 热压纳米压印对压印聚合物的要求 | 低玻温、粘收,好抗 |
较低的 玻璃化转变温度、较低的 粘塑性、较小的 收缩性、较好的 抗刻蚀性 |
6 | 列举常用的沉积图形转移法 | 薄脱双镀,嵌模喷掠 |
薄膜沉积技术、溶脱剥离法、电镀法、化学镀、嵌入法、模板法、喷墨打印法、掠角沉积法 |
7 | 对反应等离子体刻蚀有决定性影响的参数 | 流功温压,电极气体 |
反应气体流速、放电功率、反应室气压、样品材料表面温度、电极材料、辅助气体 |
8 | 常见的间接加工技术 | 侧垂双横,超纳 |
侧壁沉积法、垂直抽减法、横向抽减法、横向添加法、纳米球阵列法、超级分辨率法 |
新人制作,如有错误,欢迎指出,感激不尽!
欢迎关注公众号,会分享一些更日常的东西!
如需转载,请标注出处!
Recommend
About Joyk
Aggregate valuable and interesting links.
Joyk means Joy of geeK