
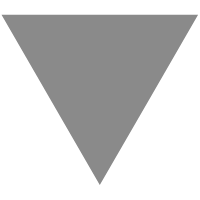
Condition Monitoring: A Pillar of Industry 4.0
source link: https://dzone.com/articles/condition-monitoring-a-pillar-of-industry-40
Go to the source link to view the article. You can view the picture content, updated content and better typesetting reading experience. If the link is broken, please click the button below to view the snapshot at that time.
Importance of Condition Monitoring in Industrial 4.0 Era
Traditional manufacturing relies on manual health checks or scheduled maintenance checks to optimize productivity. Facing a growing shortage of workers, manufacturing is forced to become leaner and rely more on connected solutions to meet demands with desired quality at competitive price points. With Industry 4.0, the focus is shifting to improving operational efficiencies through automation. And condition monitoring solutions are front and center among the key IIoT technologies behind Industry 4.0. They leverage predictive and cognitive analytics as well as machine learning to automate and streamline preventive maintenance.
Simply put, Condition Monitoring refers to monitoring parameters that reflect the health of a machine or asset. The condition data is ingested using IIoT technologies and analyzed for Predictive Maintenance purposes. However, Product Quality Control is not the only benefit that condition monitoring systems offer.
Different Industries in Which Condition Monitoring Is Used:
A few of the applications of Condition Monitoring solution across different industries include:
- Manufacturing: Equipment and machinery that handle hazardous material and are hard to reach for manual inspection can be managed through an IIoT based Condition Monitoring solution. One example includes gauges that measure the density of asphalt that carries radioactive material, or need to be closely monitored for cracks, misalignment of parts, etc. Also, monitoring the quality of engine oil can help flag the condition of the engine.
- Factories: Vibration data can be critical for rotating equipment as in presses, rolling mills used in paper and steel factories.
- Oil Companies: Oil rigs employ a network of sensors to monitor leaks, temperature of drills, pressure in storage tanks, etc.
- Logistics and Supply Chain: Delays and interruptions due to accidents and failures can impose a huge loss to the business. Vehicle Condition Monitoring systems can help monitor and track different vehicle performance attributes which would ultimately help avoid unexpected breakdowns.
- Renewable Energy: We all know a lot of efforts are made by global organizations in focusing to build and develop ways to produce green and sustainable energy, whilst finding ways in moving away from fossil fuel and non-renewable energy production. In doing so, power plants need to track the health of turbines and every moving part inside the equipment, which is a complex piece of technology.
- Food Processing: Storage conditions are very critical in food production and processing. A minor fluctuation in parameters like temperature and humidity condition can lead to food pollution and wastage.
How Is the Condition Monitoring System Implemented?
Implementing a Condition Monitoring solution means much more than just using new test instruments. It means signing up for a culture shift: from Preventive Maintenance to Predictive Maintenance. In order to reap all the benefits of Condition Monitoring, it starts with management vision and commitment and requires investments on multiple fronts: from provisioning the right equipment, to training technicians to perform investigative work based on data points, and taking consistent and timely actions across the organization.
Implementing a Successful Condition Monitoring Program Requires:
- Identifying critical assets that need to be monitored and potential risks related to their operation
- Collecting Condition Monitoring Data with the same test instruments measuring same set of attributes
- Training technicians to interpret and report Condition Monitoring data
- Identifying the corrective actions to be taken when Condition Monitoring data indicates anomalies
Ultimately, a Condition Monitoring solution visualizes the findings of condition data and sends alerts and notifications when the situation deviates from the norm.
Benefits of Condition Monitoring Solutions:
Here are some of the advantages that manufacturing companies can derive from the data collected through condition monitoring solutions, that are collectively fueling Industry 4.0 revolution:
- Product design improvements
- New product development
- Maximize production output through outage prevention
- Planning and implementing smart maintenance
- Reduce maintenance costs through effective incident management
- Extend the lifespan of the equipment through machine condition monitoring
- Optimize inventory of spares by prolonging equipment life
- Focus on preserving safety by avoiding grave malfunctions which can lead to serious environmental disasters along with legal and financial repercussion
Recommend
About Joyk
Aggregate valuable and interesting links.
Joyk means Joy of geeK