
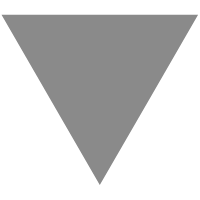
MEDLI2, the Sensors That Monitored the Perseverance Rover’s Landing on Mars
source link: https://www.allaboutcircuits.com/news/MEDLI2-sensors-monitored-perseverance-rovers-landing-mars/
Go to the source link to view the article. You can view the picture content, updated content and better typesetting reading experience. If the link is broken, please click the button below to view the snapshot at that time.
News
MEDLI2, the Sensors That Monitored the Perseverance Rover’s Landing on Mars
February 25, 2021 by Rushi Patel
The MEDLI2 sensor package on the Perseverance rover is not only gathering data for future missions; it's also demonstrating how commercial-off-the-shelf parts can be used in space.
Last week, NASA successfully landed the Perseverance rover in the Jezero Crater on Mars.

A high-level depiction of how the entry, descent, and landing (EDL) system functioned to safely land the rover on the Martian surface. Image used courtesy of NASA/JPL-Caltech
Because NASA's key goals with this mission are to acquire data on the unknowns of Mars—atmospheric conditions, landscape, and microbial life, for instance—NASA outfitted the rover with a host of sensors, many of which are commercial-off-the-shelf components.
One kit of sensors on Perseverance's heatshield, known as the MEDLI2, is designed to measure the entry, descent, and landing (EDL) of the rover to better aid future missions.
The Challenges of Designing for Space
We recently discussed the design challenges of powering the Perseverance rover from afar. But flight sensors experience their own challenges during space travel and landing.
In space, sensors need to survive fluctuating extreme temperatures, random vibrations, shock, vacuum, and ionizing radiations. For these reasons, components purpose-built for spacecraft must be tested and qualified by performing applicable environmental tests.
Inertial measurement units (IMU), gyroscopes, magnetometers, thermocouples, and pressure transducers are commonly-used sensors in deep space probes. NASA engineers must conduct extensive environmental and lifecycle testing to validate their reliability and ruggedness for the space environment. Typically, the systems are also designed conservatively with safety margins and backup/redundant units in place to increase reliability and minimize risk.
Designing and manufacturing space-grade avionics can be notably different from commercial products. For instance, printed circuit boards cannot use pure tin-based solder in the vacuum of space, which could induce catastrophic mechanical stress. Further, tin-based solder may produce "tin whiskers," which are electrically-conductive and can cause arcing. Tin whiskers can be especially hazardous in spacecraft without the ability to replace the PCBs once the payload launches.

An image of the different shapes and features of metal or tin whiskers. Image used courtesy of NASA
Still, NASA was able to use some commercial components in MEDLI2 without consequence.
The Details of MEDLI2
MEDLI2 is the second version of NASA's entry, descent, and landing instrumentation. This instrumentation package includes three types of sensors located on the backshell and heatshield of Perseverance, including 17 pressure transducers, 17 thermal plugs, and 3 heat flux sensors. Its purpose is to gain data on critical aerodynamic, aerothermodynamic, and thermal protection system (TPS) performance parameters during the EDL.
Collecting Flight Data
Previously during the MSL mission, the original MEDLI did not measure heat flux in the backshell, so flight data for this phase was among the many firsts with this new mission. The new MEDLI can collect data on:
- Reconstructed aerodynamic drag
- Vehicle attitude
- In-situ atmospheric density
- Aerothermal heating
- Transition against turbulence
- In-depth TPS performance/TPS ablation

MEDLI2 includes sensors, electronics, and harnessing, which are installed on the Mars 2020 heatshield. Image used courtesy of NASA/JPL-Caltech
This data will allow researchers to compare flight data with predicted data and update analytical models.
Gearing Up Against Heat Flux
Heat flux sensors are vulnerable to high mechanical and thermal stress, which can severely affect their functionality. MEDLI2 tested commercially-available heat flux gauges for accuracy and survivability. The candidates for the sensor kit included Gardon gauges, a thermopile, and Schmidt-Boelter gauges.

Locations of various sensors on the MEDLI2 heatshield and backshell. Image used courtesy of NASA
NASA performed benchtop tests (environmental tests with aerothermal loads) on the functionality and ecological impact of each of these gauges. The engineers ultimately chose Schmidt-Boelter gauges because of their performance during testing.
Aiming for Accuracy With Hypersonic Pressure Transducers
Hypersonic stagnation pressure is measured using a pressure transducer for the 0–35,000 Pa range that spans the entire test period, including the peak dynamic pressure environment.
One of the key findings from MEDLI was that the hypersonic pressure transducers do not provide sufficient accuracy at lower pressures during supersonic flight. Therefore, in MEDLI2, it was necessary to include a separate set of supersonic transducers that are accurate over the 0–7000 Pa range. Another pressure transducer is located on the vehicle's backshell to measure low pressures of 0-700 Pa.
Learning from MEDLI2 for Future Mars Missions
How exactly did the MEDLI2 fare during Perseverance's entry last week? NASA reports that the sensors successfully indicated heating and pressure dynamics as the entry vehicle passed through the Martian atmosphere. MEDLI2 continued collecting data after the spacecraft reached peak heating (up to 1300°C) and peak pressure. During the final 100 seconds of the entry, the vehicle remained in the supersonic flight phase.

Comparison of instrumentation sensors used in MEDLI and MEDLI2. Image used courtesy of NASA
From the wind speed, the MEDLI2 pressure transducers then collected data on direction and vehicle performance. MEDLI2 used many other sensors to gain more relevant data based on the missing details from past missions as well. NASA hopes insights obtained from this mission will eventually drive the design of crewed missions to Mars.
JPL (Jet Propulsion Laboratory) recently stated that some of the high-definition cameras used in this mission were commercial-off-the-shelf (COTS) parts, which opens the possibility of commercial sensors being used in future missions. It's possible that NASA may balance radiation-hardened and COTS components in other future projects as well.
Recommend
About Joyk
Aggregate valuable and interesting links.
Joyk means Joy of geeK