
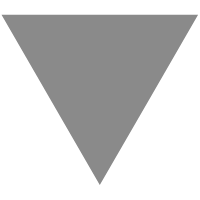
Getting Started with SAP DMC
source link: https://blogs.sap.com/2022/08/31/getting-started-with-sap-dmc/
Go to the source link to view the article. You can view the picture content, updated content and better typesetting reading experience. If the link is broken, please click the button below to view the snapshot at that time.
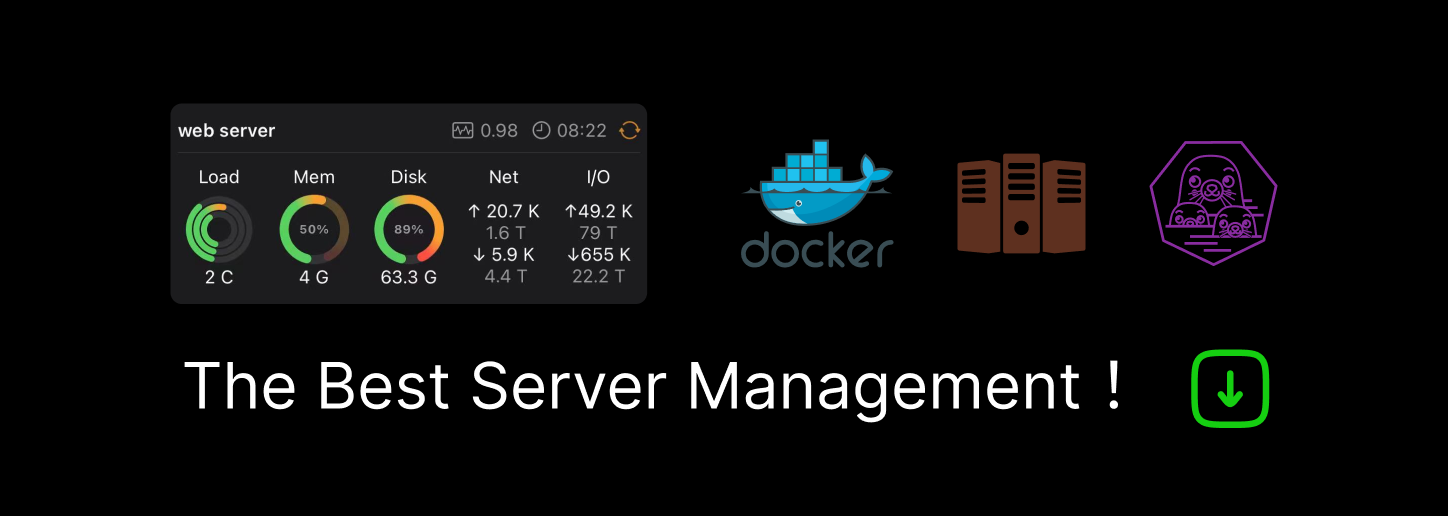
Foreword
There is a lot of interest lately in how to get started conceptually with SAP DMC so here’s a guide that can help. It will provide alignment with the current product strengths, and also links to key areas in our documentation that will help to outline how to drive your project.
Phase #1 – Stakeholders and their Role(s)
When kicking off any project with SAP in the Digital Supply Chain portfolio, and specifically for Manufacturing, the very first step is to outline business goals and objectives across the different verticals of your supply chain and understand their potential value. The people providing feedback will eventually become the key stakeholders of your project deliverables and will help to communicate value of the project later, so be sure to keep the dialog open and continuous. Typical stakeholders in manufacturing are most commonly the Plant Managers, Supervisors, and Operations teams that will be interacting with the system on a daily basis. However, additional roles to consider are warehouse, quality, planning and maintenance leads as at a functional level they will all play a role both upfront in for the integration but also help to identify process nuances (aka customizations).
Once this is complete, you will have a list that ties core topics of the project to various aspects of your business such as quality/yield, planning, maintenance, inventory, labor, ANDON displays. There is a strong possibly other technology centric topics such as system scalability, reduction of software systems, data visibility and reporting (tactical & strategic), and increased process automation. Each of these topics should then be ranked and coupled together to create your project milestones. Starting with the sequence of the project and then overlaying the business value provided for each and then ranked according to overlapping value to identify key milestones for stakeholder review.
That sounds easy enough, but to quantify “value” you have to know the production processes which benefit from the topics the most. You also have to ensure that the location of these production processes is ok with undertaking a project around continuous improvement and adoption of Industry 4.0 to help them along. Take special note that this is a combination of software, hardware and people all working together and supporting the various aspects of scope for the project. They will be the champions providing feedback for their respective topics at various milestone dates throughout your project and should also be supporting the business value of the topic horizontally and vertically within the organization.
Phase #2 – Key Points for Delivery & Adoption
Once the ranking priority is outlined and the ‘core’ of what is needed to show the end to end process is stable, there needs to be a feasibility check to ensure that operations doesn’t feel burdened by the interface. The key thing to remember is that while collecting data in software is cool, if you make people do too many things they will reject the solution. This is where the timeline for delivery meets the end users that are going to be working with the offering every day so if this isn’t a positive handoff then there are going to be adoption and rollout problems all over the place.
As part of the project plan be sure to communicate the key milestones and delivery dates as proof points for the stakeholders and reserve the calendars early. Technical functionality around the system working as expected and also feasibility checkpoints should be performed to ensure adoptability. This is often where the system will require data that operations has not typically had to provide and requires manual data collection to move the process (i.e. Quality Inspection Results). If you have smart tools already, an integrated SCADA, or budget to invest in hardware this is where you can leverage these systems to drive the process for you. These will be identified up front as ground up plant investments and also will show up in spaces that were lesser known so just plan for this need up front in small scale and look to build on top of it. The SAP DMC environment has a tool designed to support this adoption called Production Process Designer and the more automated you can make the data collection and drive the SAP DMC (MES) processes the better the adoptability will be.
Phase #3 – Review and Leverage Standard Content
Implementation of SAP DMC is a ‘reverse’ approach from a traditional MES environment. This is because the implementation starts with the integration to SAP ERP to set the foundation for master and transactional data (SAP DMC Integration Guide). This means that not all setup information will be done within SAP DMC alone but rather you will see configuration in Material Master, Quality Management, Production Planning (-PI), Plant Maintenance, and also in Extended Warehouse Management. Please plan resources out early on in the project that will help as you along the way to understand how to configure these integrated systems to best fit the processes that are outlined in manufacturing. In short, if you have a process that ‘seems backward’ it probably is and now is a good time to clean that up so that it makes more sense logically rather than just going with the “That’s how it works today…” approach. The transformation isn’t about what you have done before it’s about making it better and leveraging this project as a way to do just that is a good use of time.
The SAP DMC ecosystem is growing and with each release there are new features and content functionality and integration with ERP processes. You can track each release and functional area within SAP DMC Help by going to the published What’s New Viewer. Here you will find details on what was actually released in the quarterly development cycle. If you can’t find something you’re looking for you can also consult the SAP DMC Roadmap Explorer to see if it was moved out in the release timeline. Another great project booster is the SAP DMC Implementation Starter Kits which provide documentation and content for how to setup various scenarios which are core to SAP DMC and will likely already be part of your project scope. Starting with the kit documentation and building from there is a good way to ensure that you’re starting in the right place and have aligned the right people to help with the definition.
Closing Remarks
The above may see pretty straight-forward but the approach is not often followed. I see many projects with the mentality of replacing the existing how it worked in the past set of processes and then trying to overlay them into the new SAP DMC MES. This can work in some cases but often will run into issues with how the business and integrated systems need the manufacturing operations layer to run in order to provide efficiency of optimized planning and ensure material availability across the plant. Let the MES layer do what it is intended to do (Good read from the ISA team) and leverage the power of production to be the heartbeat that powers the veins of your supply chain.
Recommend
About Joyk
Aggregate valuable and interesting links.
Joyk means Joy of geeK