
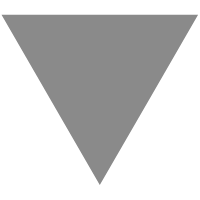
The Differences between Traditional and Event-based WIP and Variance Calculation
source link: https://blogs.sap.com/2022/05/03/the-differences-between-traditional-and-event-based-wip-and-variance-calculation/
Go to the source link to view the article. You can view the picture content, updated content and better typesetting reading experience. If the link is broken, please click the button below to view the snapshot at that time.
The Differences between Traditional and Event-based WIP and Variance Calculation
Shuge Guo has already written two excellent blogs to introduce event-based production accounting in SAP S/4HANA Cloud and to explain how the new approach fits into the context of universal parallel accounting. As more organizations embark on their digital transformation, I want to focus on what changes when you move from the traditional approach with the period-based calculation of work in process (WIP) and variances to the event-based approach, which is now the default setting in SAP S/4HANA Cloud and compulsory if you work with universal parallel accounting. The settings for the traditional approach are delivered with Scope Item BEI (Period-End Closing – Plant) and for the new approach with Scope Item 3F0 (Event-Based Production Cost Posting). My aim is to revisit some of the basic concepts and then show the accounting impact within each approach and the settings that control these journal entries.
Traditional Approach to WIP and Variance Calculation
If you’ve worked with production orders in SAP ERP, you are probably already familiar with the traditional approach, where WIP calculation and variance calculation are period-close activities that calculate and update the values for WIP and variances and store them in the CO tables, then rely on settlement to create the journal entries to capitalize the work in process or record the production variances as part of the period gains or losses. You can calculate WIP and variances as often as you require during the period, but you can only settle once in any accounting period.
With the simplified data model introduced for SAP S/4HANA financial accounting and controlling moved into the universal journal and there is no longer a separate data store for Financial Accounting and Controlling, but rather one journal entry for each business transaction (goods issue, confirmation, goods receipt). The issue of raw materials to the production order results in a single journal entry, the confirmation of production activity in a second journal entry, and the delivery of the finished goods to stock in a third journal entry, each with a reference document that provides the link back to the triggering application. However, work in process is not capitalized automatically and reversed when the order is complete but must still be calculated and the associated journal entry triggered via settlement to record the work in process on the balance sheet. Likewise, the production variances are not assigned to the various variance categories automatically but must be calculated and a journal entry triggered via settlement to record any remaining costs on completion as production variances.
Figure 1 shows the traditional status-driven approach. The close transactions select all open production orders to determine whether the remaining costs on the order are to be considered work in process or production variances.
- If the order has been completed (status DLV) or technically closed (status TECO), then all remaining costs on the order are considered production variances and the goal is to explain the source of these variances.
- If the order has been started (status REL) or partially delivered (status PDLV), then the remaining costs on the order are considered work in process (or WIP). As the name implies, work in process is a temporary state and will be reversed when the goods are delivered to stock.
Settlement is used to create journal entries for the WIP calculated for the open orders and the production variances calculated for the closed orders at period close.

Figure 1: Traditional Approach
The business reason to consider a move from the traditional approach to the event-based approach is obviously to provide management information during the period rather than at period close, but there is also a technical reason. The calculated WIP and variances are not stored in the universal journal, but rather in the legacy table (COSB) and this table does not support ledgers and only has two currencies. As you look to future-proof your approach to production accounting, it is therefore worth considering a change of approach.
You’ll see the multiple data stores reflected in the different reporting layouts if you view the costs of a production order either from within the production order or using transaction KKBC_ORD. There you switch between the journal entries relating to the production order (sourced from the universal journal) and the WIP and variances calculated for the production order by switching between the report layouts, as shown in Figure 2. The work in process shown in layout 1SAP03 (work in process) and the target costs shown in layout 1SAP01 (target/actual – comparison) aren’t being pulled from the universal journal, but rather from a separate table (COSB).

Figure 2: Layouts for Production Order
At period close, you must run WIP calculation to determine the value of the work in process for all open production orders. The result of WIP calculation according to the traditional approach is shown in Figure 3, where we see both the cumulative WIP (the work in process collected over the lifetime of the production order) and the periodic WIP (the change to WIP in the relevant accounting period) for each order. The periodic WIP is settled to the balance sheet. Here we see that there is a two stage procedure to first calculate the WIP and store the results in the CO tables and then move the WIP to Financial Accounting using settlement.

Figure 3: Result of WIP Calculation
The total value for the work in process can be broken out and stored on separate results analysis cost elements to reflect various groups of costs, as shown in Figure 4.

Figure 4: Reporting of WIP by results analysis cost elements
With the new approach, by contrast, the separate data store behind Figures 3 and 4 does not exist and the system triggers a journal entry with every business transaction that increases or decreases WIP, and this value is shown immediately in the Event-Based Order Costs app. Results analysis cost elements are not needed in the new approach.
At period close, you must run variance calculation to determine the value of the production variances for all completed production orders. The result of variance calculation according to the traditional approach is shown in Figure 5, where we see the total variances for the order in the top line of the report and the variance categories for each input and output in the report below it. Again, these variances are stored in the CO tables and then moved to Margin Analysis, Actual Costing and Financial Accounting using settlement.

Figure 5: Result of Variance Calculation
Finally, settlement clears the costs on the production order, moves the WIP to the balance sheet and the production variances to the profit and loss statement. The result is the settlement document shown in Figure 6. The production variances have been assigned to the material account (receiver MAT) and to margin analysis (receiver PSG). Settlement also triggers a journal entry to clear any remaining WIP on the order.

Figure 6: Result of Settlement
To see the result of settlement, you must view the settlement document or the financial statements, where you’ll find journal entries for the settled work in process and production variances.
New Approach to WIP and Variance Calculation
Figure 7 shows the lifecycle of a production order, from creation to final delivery. The process of issuing raw materials to the production order, confirming production activity, and delivering the completed goods to inventory remains the same with the new approach. If you choose to work with scope item 3F0 (Event-Based Production Cost Posting) rather than the more familiar BEI (Period-End Closing – Plant) in SAP S/4HANA Cloud, a journal entry for work in process is created as soon as raw materials are issued to the order or production activity confirmed. There is no need to calculate work in process and move it to financial accounting, as this happens automatically. When the finished goods are delivered to stock, these goods are valuated at standard cost and the order is credited with this value. At this point the work in process for the delivered goods is cancelled and a new journal entry created for the reduction. Finally, when all finished goods have been delivered to stock, any remaining WIP is cancelled, and a journal entry created for the various production variances. Notice also that material overhead and production overhead are also charged immediately rather than at period-close.

Figure 7: Event-based Approach
In this blog, I’ll use a production order to walk you through the various journal entries, but you can also work with process orders and make-to-order production. The supported manufacturing scope items are listed in the documentation for scope item 3F0. The approach is not yet supported for repetitive manufacturing and engineer-to-order. In this example, we’ll use a simple production order with two operations. We’ll start by confirming the first operation. In Figure 8 we see the line items for the confirmation and goods issues to the operation as before. The fundamental change is that additional journal entries are created to reflect any overhead and WIP and that these link to the reference document for the underlying business transaction (the event). An overhead charge is applied immediately to capture the follow-up costs for the overhead, then a further journal entry is created for the work in process. This creates work in process for the raw material costs plus the material overhead and the production activity costs plus the production overhead. Notice that compared to Figure 2 there is no need to shift between layouts to view the actual costs and the work in process and that the WIP line appears in the same view as the input costs on the production order. While organizations in SAP ERP used the results analysis cost elements shown in Figure 4 to break out their WIP for reporting purposes, here you can see the breakdown of the costs into raw materials, internal activity and overhead in the same report.

Figure 8: Event-Based Order app, Showing Actual Costs and WIP
You can view all journal entries in the Display Line Items app shown in Figure 9. Here we have selected the G/L account for the raw materials to show the various goods issues to the production order. Notice the reference document, since this provides the link to the follow-on processes.

Figure 9: Line Items for Goods Issues to Production Order
The goods issue (notice the reference document) has also triggered a journal entry for material overhead with the business transaction type KZPI, as shown in Figure 10. The configuration settings are made in the costing sheet as in the traditional approach, but a material overhead posting is made whenever goods are issued to the production order under the accounts contained in the costing sheet. If we were to create a second material document to issue further raw materials to the production order, this would trigger the creation of a second material overhead document. This can result in significantly more accounting documents than when material overhead is calculated in total at period close.

Figure 10: Line Item for Material Overhead
You can identify line items for work in process by the business transaction type EBWP shown in Figure 11. Notice that there are two line items, one for the material-related WIP (notice the reference document again) and one for the production-related WIP.

Figure 11: Line Item for WIP at First Operation
Alternatively, you can display the work in process in the Event-Based Work in Process app shown in Figure 12 where we see the work in process for our production order and also the estimated cost to complete (the remaining planned costs for the production order). This is a nice innovation to indicate how close to completion the production order is. We have yet to confirm the production activities at the second operation and can see this reflected in the app.

Figure 12: Event-Based WIP app
We will now continue the process and confirm the final production activity and deliver the finished goods to stock. This results in additional costs for the production activities (the cost to complete from Figure 12) and a journal entry for the goods receipt in Figure 13. The WIP shown in Figures 11 and 12 is cancelled and the balance on the production order is treated as a production variance. Notice that there is a credit posting for the goods receipt to stock, the value in the WIP column is now zero, and there is a negative production variance. The approach for calculating input price variances, input quantity variances, resource usage variances, lot size variances, and remaining variances does not change with the move to event-based production accounting, but the timing is different with the variances being calculated as soon as the order has the status finally delivered or technically complete rather than at period close. Be aware, however, that it is not currently (CE 2202) possible to take planned scrap into account or to calculate output variances for differences in lot-size.

Figure 13: Event-Based Order app, After Confirmation of Final Operation
Figure 14 shows the journal entries for the original work in process, the new work in process for the second production confirmation (notice the different reference document) and the reversal posting that reflects the fact that the work in process must be cancelled since the goods have been completed and moved to finished goods inventory.

Figure 14: Line Items for WIP, Showing Creation and Cancellation
Figure 15 shows the journal entry for the production variances with the business transaction type EBVP. In SAP S/4HANA it is possible to post the production variances to separate G/L accounts for each of the variance categories. In SAP S/4HANA Cloud the journal entries for the production variances are made to a single account with the variance categories separated by SLA Line Item Type so that can each be assigned to a separate line in the Product Profitability and Production Variances app.

Figure 15: Line Items for Production Variances
Figure 16 shows how the production variances are included in the Product Profitability with Production Variances app. This shows the production variances for all products sold in the period so that you can perform a multi-level Margin Analysis.

Figure 16: Product Profitability with Production Variances app, Showing Variance Categories
Behind the Scenes
When you choose scope item 3F0 over BEI, the key difference is the results analysis key used as a default for the production orders. Figure 17 shows the results analysis key RSEBW in the production order and the flag Event-Based Posting that controls the application of the new posting logic. You cannot change the results analysis key once there are postings on the production order, so you can only introduce the logic for new orders. Shuge Guo describes the transition approach in the context of universal parallel accounting in her blog (link at end).

Figure 17: Results Analysis Key in Production Order
The other difference is that instead of the familiar settlement rule, we now have a posting rule as shown in Figure 18, that assigns the costs for the production order to the material as a receiver. It is also possible to assign costs to a cost center, a WBS element or an order, if you have production orders whose materials should not be delivered to stock and capitalized as finished goods inventory.

Figure 18: Posting Rule in Production Order
Figure 19 shows the settings associated with the results analysis key, including the variance categories to be calculated and the receivers allowed in the posting rule. In the traditional approach, the active variance categories are controlled by the variance key and target cost version and the allowed receivers are controlled by the settlement profile. Event-based orders do not have a variance key.

Figure 19: Settings Behind Results Analysis Key
When you work with the traditional approach to WIP calculation, the source costs on the order are assigned to line IDs. With the new approach, this grouping is represented by the sources shown in Figure 20. The sources are fixed, but you can assign your own G/L accounts to these sources when you configure your solution. All input costs assigned to these sources are capitalized as WIP and there is no option to define some costs as non-capitalizable, as in the traditional approach.

Figure 20: Assigning Costs to WIP Sources
In the traditional approach to WIP calculation the values calculated and stored in Controlling are mapped to G/L accounts for work in process and reserves for unrealized costs. Now you can enter the P&L and BS accounts for the creation and reversal of the WIP for each source as shown in Figure 21. Again, you can enter your own accounts when you configure your solution.

Figure 21: Defining WIP Accounts
Closing Comments
The new approach to WIP and variance calculation is only available in SAP S/4HANA Cloud and shows SAP’s continued work to simplify business processes and remove tasks from the period close. It is planned to deliver the new approach in SAP S/4HANA with release OP2022 in combination with the business function for universal parallel accounting.
You can find more information on the cloud approach in these two posts together with advice on how to move from the traditional to the event-based approach.
Event-Based Production Cost Posting
Production Accounting for Universal Parallel Accounting
If you are new to the topic, you may also find the information in my book helpful.
Recommend
About Joyk
Aggregate valuable and interesting links.
Joyk means Joy of geeK