
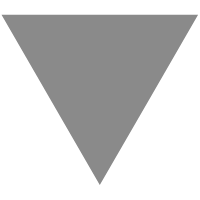
Robotics in Manufacturing and Production
source link: https://codecondo.com/robotics-in-manufacturing-and-production/
Go to the source link to view the article. You can view the picture content, updated content and better typesetting reading experience. If the link is broken, please click the button below to view the snapshot at that time.
Robotics in Manufacturing and Production
Robotic automation has made its way into several areas in manufacturing. Welding, assembly, transportation, raw material handling and product packaging are all jobs performed by robots. Robotic automation is being used by an increasing number of manufacturers for a broader range of applications.
Manufacturing robots play a variety of responsibilities. Fully autonomous robots are often used in manufacturing for high-volume, repetitive procedures, where a robot’s speed, precision and durability provide unrivalled benefits. Other factory automation ideas include robots that assist humans with more difficult jobs. The robot performs process components such as lifting, holding and moving large objects.
Why is robotics being used in manufacturing and production?
- Time-saving
Robots can be installed in a fraction of the time and at a fraction of the cost that they could in earlier decades. Prices have dropped considerably as a result of increased sales. Robots have built-in state-of-the-art facilities, quality advancements and controlled safety requirements, which lead to labour cost savings and unplanned downtime. Robots may also work around the clock, improving output while decreasing downtime.
- Creation of jobs
All of the following skills are required: programming, engineering, end-effector design, operators, data analysts, robot production and systems integration. Humans are required to assist in the maintenance of the machines. Robots enable firms to reduce costs and re-locate employment to the United States, resulting in more jobs for American employees. Robots also prevent people from having to conduct repetitive, dull and harmful duties that might jeopardise their ability to work.
Robotic automation provides firms with ever-increasing options to save costs, improve productivity and remain competitive. Return on investment may equal growth, which not only raises earnings but also provides employment and savings for clients.
- Programming has become easier than before
To train robots, one no longer has to understand sophisticated programming languages. There are two simple approaches to teaching modern robots. The first way, offline programming allows a user to model an entire cell or work area and construct a task’s sequence of moves.
A teach pendant is the second method for teaching robots. A programmer or engineer merely directs the robot through a series of steps. The instructions are saved after some fine-tuning. The robot carefully runs through the programme, checking for clashes with objects or humans. After several good test runs, the robot can now function at full speed.
How is robotics being used in manufacturing and production?
- Robots are rapidly being employed to handle a diverse range of things, ranging from blood samples to huge containers, specifically, items and materials that require stability or harmful ones that might cause contamination if they come into touch with humans.
The robots never tire or make mistakes while executing their primary role and this approach also decreases the risks of endangering the lives of human employees. More labour is done by robots, and fewer employees are needed to supervise the process.
- Robotic welding equipment automates the welding process by conducting the weld and handling the workpiece directly. Welding robots are often employed in arc and spot welding processes where precision and speed are required. Because of their precision, they are widely used in the automobile sector. By automating the welding process, you may achieve shorter cycle times, higher weld quality and lower labour expenses. Integrating robot welding will also make your workplace safer for your employees. Arc burns, overspray and breathing dangerous smoke will no longer be a concern for your personnel.
- Assembling product pieces is a long, repetitive activity that may be readily disturbed by a lack of judgement and a variety of other uncontrolled causes.
By substituting such a mechanism with a robot, the process is greatly expedited, and the likelihood of a mistake happening is much minimised. This also liberates up the human element of the assembly process, allowing it to focus on quantity over quality and removing it from the riskiest aspect of the process.
- Dispensing robots are strategically located near the path of the product in procedures that need glue, paint or sprays to be sprayed to a surface. This is another example of a repetitious task that a robot can handle better than a human worker owing to the absence of mistakes.
- Certain items must go through a certain form of processing before they can be sold, such as carving, polishing or sawing. This job is performed by robots with varying levels of autonomy, depending on the intricacy of the task and the robot’s capabilities.
- Industrial paint robots are generally used in the automobile sector to uniformly paint components and equipment while leaving no paint stains or drips. They are exact and apply the appropriate amount of paint to each piece of machinery without wasting any supplies. Paint robots have lately been utilised to replicate original paintings outside of the automobile sector. Incorporating painting robots will enhance your total job quality by providing high-quality outcomes, saving you money on paint supplies and keeping your personnel safe from a potentially dangerous painting work environment.
Industrial painting machines are programmed to be tiny enough to reach regions and holes that would be difficult and complicated for human employees to access. Painting robots may also fit in compact spaces and conserve floor space due to their thin form. To reduce space in manufacturing, they can be placed on walls, shelves or tracks.
Conclusion
Robots are an indispensable aspect of today’s production world. Some company owners and plant managers prefer to choose robotic integration as a method of automation. The benefits of incorporating robotics into your manufacturing line are limitless. Industrial robots are capable of performing repetitive, time-consuming operations with precision and regularity. Robots will not only be able to work quicker and for longer periods of time, but they will also be able to enhance production rates and generate new employment. Big decisions, on the other hand, need investigation and comprehension. Incorporating robotics into your workplace necessitates investment, evaluating your projected ROI and accepting changes and constraints.
Also Read: Different Applications of Humanoid Robots Now and in the Future
Recommend
About Joyk
Aggregate valuable and interesting links.
Joyk means Joy of geeK