
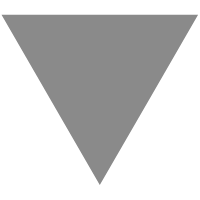
Haber-Bosch And The Greening Of Ammonia Production
source link: https://hackaday.com/2022/01/11/haber-bosch-and-the-greening-of-ammonia-production/
Go to the source link to view the article. You can view the picture content, updated content and better typesetting reading experience. If the link is broken, please click the button below to view the snapshot at that time.
Haber-Bosch And The Greening Of Ammonia Production
We here on Earth live at the bottom of an ocean of nitrogen. Nearly 80% of every breath we take is nitrogen, and the element is a vital component of the building blocks of life. Nitrogen is critical to the backbone of proteins that form the scaffold that life hangs on and that catalyze the myriad reactions in our cells, and the information needed to build these biopolymers is encoded in nucleic acids, themselves nitrogen-rich molecules.
And yet, in its abundant gaseous form, nitrogen remains directly unavailable to higher life forms, unusably inert and unreactive. We must steal our vital supply of nitrogen from the few species that have learned the biochemical trick of turning atmospheric nitrogen into more reactive compounds like ammonia. Or at least until relatively recently, when a couple of particularly clever members of our species found a way to pull nitrogen from the air using a combination of chemistry and engineering now known as the Haber-Bosch process.
Haber-Bosch has been wildly successful, and thanks to the crops fertilized with its nitrogenous output, is directly responsible for growing the population from a billion people in 1900 to almost eight billion people today. Fully 50% of the nitrogen in your body right now probably came from a Haber-Bosch reactor somewhere, so we all quite literally depend on it for our lives. As miraculous as Haber-Bosch is, though, it’s not without its problems, particularly in this age of dwindling supplies of the fossil fuels needed to run it. Here, we’ll take a deep dive into Haber-Bosch, and we’ll also take a look at ways to potentially decarbonize our nitrogen fixation industry in the future.
Easy to Find, Hard to Use
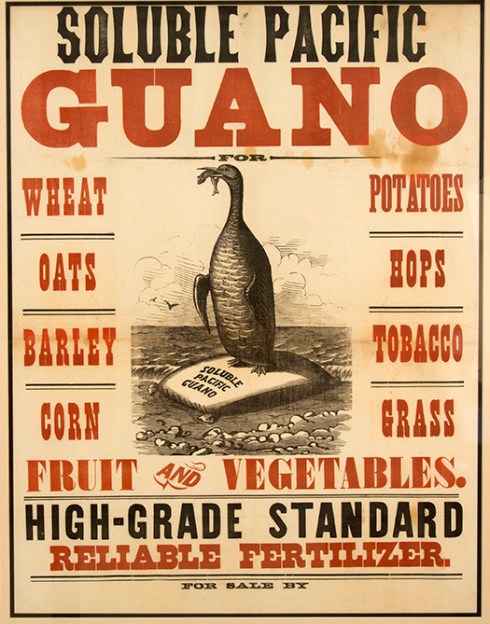
The heart of the nitrogen problem, and the reason why the production of ammonia is both necessary and so energy-intensive, stems from the nature of the element itself, specifically its tendency to bond strongly with others of its kind. Nitrogen has three unpaired electrons available for bonding, and the triple bond that results in the diatomic nitrogen that makes up most of our atmosphere is very difficult to break.
These triple bonds are what make gaseous nitrogen so inert, but it also creates a problem for the organisms that need elemental nitrogen to survive. Nature has found a number of hacks to that problem, through nitrogen-fixing processes, which use enzymes as catalysts to convert diatomic nitrogen into ammonia or other nitrogenous compounds.
Nitrogen-fixing microorganisms make nitrogen bioavailable up and down the food chain, and for most of human history, natural processes were the only method of obtaining the nitrogen necessary for the fertilization of crops. Mining of deposits of nitrogenous compounds, such as saltpeter (potassium nitrate) or in the form of guano from bat and bird droppings, was once the primary source of nitrates for agriculture and industry.
But such deposits are relatively rare and finite in extent, leading to a problem both in terms of feeding a rapidly expanding world population and providing them with the products needed for an increased standard of living. This led chemists to search for methods of turning the vast reserves of atmospheric nitrogen into usable ammonia, starting at the end of the 19th century. While there were several successful contenders, German chemist Fritz Haber’s laboratory demonstration of making ammonia from air became the de facto process; once it was scaled up and industrialized by chemist and engineer Carl Bosch, the Haber-Bosch process was born.
Under Pressure
The simple chemistry of the Haber-Bosch process belies its complexity, especially when undertaken at industrial scales. The overall reaction makes it seem quite straightforward — a little nitrogen, a little hydrogen, and you’ve got ammonia:
But the problem lies in the aforementioned triple bond in the N2 molecule, as well as in that double-headed arrow in the equation. That means the reaction can go both ways, and depending on reaction conditions such as pressure and temperature, it’s actually more likely to run in reverse, with ammonia decomposing back into nitrogen and hydrogen. Driving the reaction toward the production of ammonia is the trick, as is providing the energy needed to break down diatomic nitrogen in the atmosphere. The other trick is providing enough hydrogen, an element that is not particularly abundant in our atmosphere.
To achieve all of these goals, the Haber-Bosch process relies on heat and pressure — a lot of each. The process starts with the production of hydrogen by steam reformation of natural gas, or methane:
Steam reformation takes place as a continuous process, where natural gas and superheated steam are pumped into a reaction chamber containing nickel catalyst. The output of the first reformer process is further reacted to remove the carbon monoxide and unreacted methane and scrubbed of any sulfur-containing compounds and carbon dioxide, until nothing remains but nitrogen and hydrogen.
The two feed gasses are then pumped into a heavy-walled reaction chamber in a ratio of three hydrogen molecules to each nitrogen molecule. The reactor vessel must be extremely sturdy because the optimum conditions to drive the reaction to completion are a temperature of 450 °C and a pressure 300 times atmospheric. The key to the reaction is the catalyst inside the reactor, most of which are based on powdered iron. The catalyst allows the nitrogen and hydrogen to bind into ammonia, which is removed by condensing it into a liquid state.
The handy thing about Haber-Bosch is what Bosch brought to the table: scalability. Ammonia plants can be massive, and are often co-located with other chemical plants that use ammonia as feedstock for their processes. About 80% of the ammonia produced by the Haber-Bosch process is destined for agricultural uses, either applied directly to the soil as a liquid, or in the manufacture of pelletized fertilizer. Ammonia is also an ingredient in hundreds of other products, from explosives to textiles to dyes, to the tune of over 230 million tonnes produced worldwide in 2018.
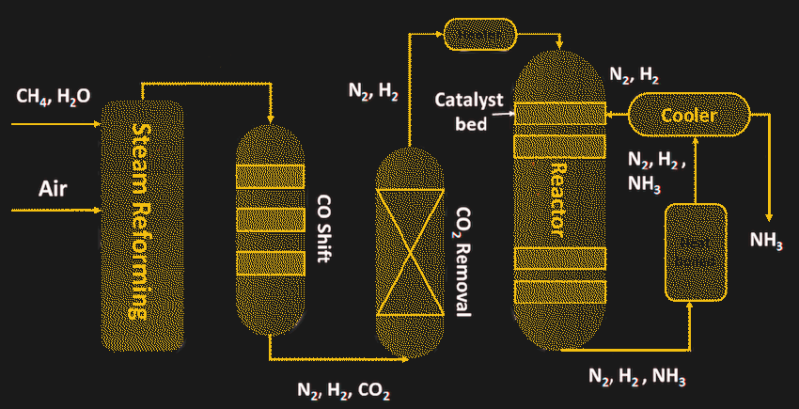
Cleaner and Greener?
Between the use of methane as both feedstock and fuel, Haber-Bosch is a very dirty process from an environmental standpoint. Worldwide, Haber-Bosch consumes almost 5% of natural gas production, and is responsible for about 2% of the total world energy supply. Then there’s the CO2 the process produces; while a lot of it is captured and sold off as a useful byproduct, ammonia production produced something like 450 million tonnes of CO2 in 2010, or about 1% of the total global emissions. Add in the fact that something like 50% of the food production is absolutely dependent on ammonia, and you’ve got a ripe target for decarbonization.
One way to knock Haber-Bosch off the ammonia pedestal is to leverage electrolytic processes. In the simplest case, electrolysis could be used to create the hydrogen feedstock from water rather than methane. While natural gas would still likely be needed to generate the pressures and temperatures needed for ammonia synthesis, this would at least eliminate methane as a feedstock. And if the electrolytic cells could be powered by renewable sources like wind or solar, such a hybrid approach could go a long way to cleaning up Haber-Bosch.
But some researchers are looking at a completely electrolytic process that will make ammonia production much greener than even the hybrid approach. In a recent paper, a team from Monash University in Australia details an electrolytic process that uses chemistry similar to that in lithium batteries to make ammonia in a completely different way, one that potentially eliminates most of the dirtier aspects of Haber-Bosch.
The process uses a lithium-containing electrolyte in a small electrochemical cell; when current is applied to the cell, atmospheric nitrogen dissolved in the electrolyte combines with lithium to make lithium nitride (Li3N) at the cathode of the cell. Lithium nitride looks a lot like ammonia, with the three lithium atoms standing in for the three hydrogens, and sort of acts like a scaffolding upon which to build ammonia. All that remains is to replace the lithium atoms with hydrogen — a feat easier said than done.
The secret to the process lies in a class of chemicals called phosphonium, which are positively charged molecules with phosphorus at the center. The phosphonium salt used by the Monash team proved to be effective at carrying protons from the anode of the cell to the lithium nitride, which readily accepted the donation. But they also found that the phosphonium molecule could go through the process again, picking up a proton at the anodes and delivering it to the lithium nitride at the cathode. In this way, all three lithium atoms in the lithium nitride are replaced with hydrogen, resulting in ammonia produced at room temperature without methane as a feedstock. The Monash process appears promising. In a 20-hour test under lab conditions, a small cell produced 53 nanomoles of ammonia per second for every square centimeter of electrode surface, and did it with an electrical efficiency of 69%.
If the method can prove out, it has a lot of advantages over Haber-Bosch. Chief among these is the lack of high temperatures and pressures, and the fact that the whole thing could potentially run on nothing but renewable electricity. There’s also the possibility that this could be the key to smaller, distributed ammonia production; rather than relying on a relatively few centralized industrial plants, ammonia production could potentially be miniaturized and brought closer to the point of use.
There are plenty of hurdles to overcome with the Monash process, of course. Relying on lithium electrolytes in a world where EVs and other battery-powered devices are already stretching the limits of lithium extraction seems tenuous, and the fact that lithium mining is heavily dependent on fossil fuels, at least for the time being, tarnishes the green potential of electrolytic ammonia as well. Still, it’s an exciting development and one that just may keep the world fed and fueled in a cleaner, greener way.
Recommend
About Joyk
Aggregate valuable and interesting links.
Joyk means Joy of geeK