
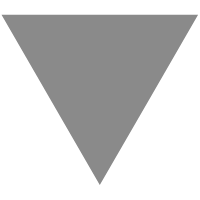
5 Tips to Consider Before Buying a New Soldering Iron
source link: https://www.makeuseof.com/tips-for-buying-new-soldering-iron/
Go to the source link to view the article. You can view the picture content, updated content and better typesetting reading experience. If the link is broken, please click the button below to view the snapshot at that time.
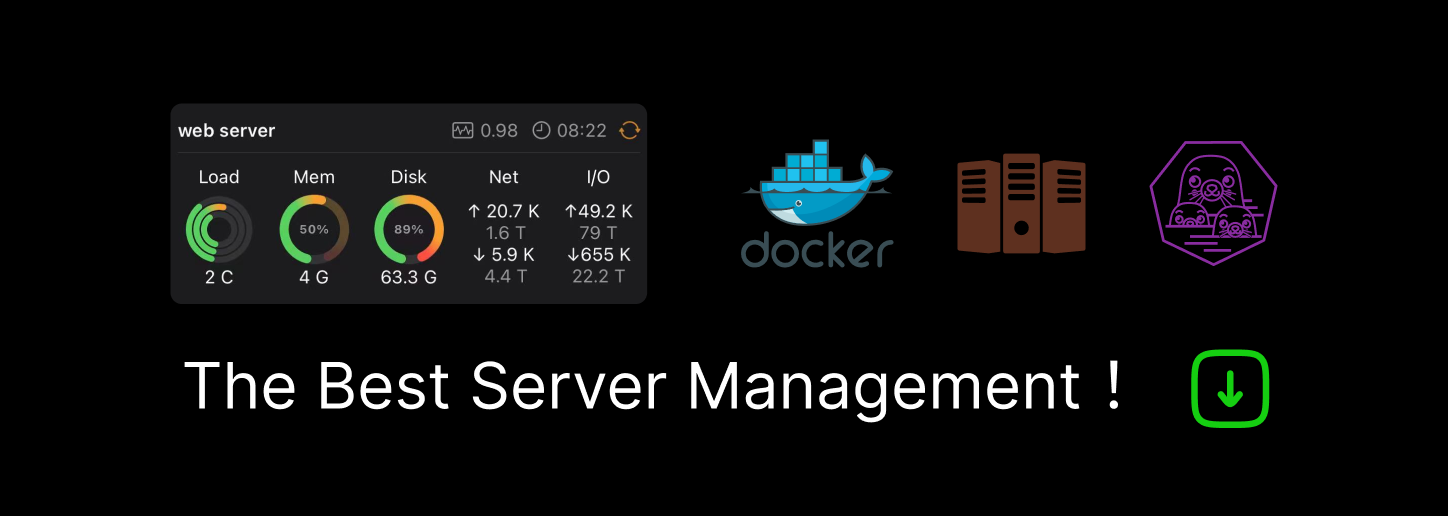
5 Tips to Consider Before Buying a New Soldering Iron
Published 5 hours ago
Tired of failing at soldering? Perhaps you’re being bogged down by substandard tools. Here’s how cheap soldering irons are priming you up for failure.
Most beginners start a new hobby with cheap tools and upgrade them as their skills improve. Soldering, however, is a discipline where a high-quality tool is the difference between a successful project and an expensive electronics barbecue party of one.
Soldering is essentially a simple skill complicated by the prevalence of cheap irons that scare away beginners. Read on to find out how you could do a whole lot better with a quality soldering iron, and why cheap ones just aren’t worth the trouble.
1. Avoid Fixed Temperature Soldering Irons
Knowing the basics of soldering is critical to understanding the difference between a good soldering iron and a bad one. Being able to tell that requires a thorough understanding of soldering mechanics, such as the metal-solvent action and the role of flux as explained in our soldering basics guide.
An ideal soldering iron must not only provide enough heat for the soldering process, but it should also do so in a precisely controlled manner. Soldering involves varying component sizes and solder types, which require specific soldering temperatures. A good iron should, therefore, allow granular control over the tip temperature.
Any mistakes in that department lead to either cold solder joints or burnt components. Unfortunately, that rules out all entry-level irons lacking temperature adjustment.
Such soldering irons heat the tip to an arbitrary preset temperature and aren’t good at maintaining it well enough. Without any means to sense tip temperature, these irons can neither reduce heater power when soldering delicate components nor can they increase it to handle larger work.
Even the most experienced folks find it nigh impossible to deliver consistent results with such irons. Beginners are quite likely to ruin their soldering projects with these tools.
2. Understanding Wattage and Temperature Control
The advertised wattage of the soldering iron essentially indicates how rapidly the heating element can raise tip temperature. An iron rated at 25 watts will take well over a minute to bring the tip up to 660°F from room temperature. On the other hand, a JBC soldering station rated at 130 watts will get there in a couple of seconds.
Soldering is a lot more complicated than simply heating the tip to the desired temperature.
When the hot tip touches the work, it dumps heat into the relatively cooler PCB pad and the component leads and becomes colder itself. This is when the heating element kicks in to maintain tip temperature. Delicate soldering jobs with smaller components equals lower thermal mass, so even a puny 25-watt iron can keep up.
However, large components such as bulk capacitors and ground planes act like heatsinks. Lower wattage soldering irons cannot replenish heat lost during soldering quick enough, which leads to cold joints and outright failure to solder components with high thermal mass.
If you intend to solder large parts such as XT-90 connectors, massive ground planes, and other high thermal mass components, you must opt for a high wattage soldering iron.
Smaller soldering jobs can be handled with low-power irons, but soldering mechanical keyboard switches is a good example of how even delicate components can benefit from high-wattage irons. A standard 104-key keyboard entails soldering hundreds of joints in quick succession.
A low-wattage iron cannot maintain tip temperature under such conditions and results in a phenomenon called thermal drift, wherein the tip temperature progressively drops until you eventually end up with cold joints. Good soldering stations are equipped with at least 60 watts of heating power, which makes them versatile enough to be used for most jobs.
Related: Cheap and Exciting DIY Electronics Projects to Tackle Under $15
Contrary to popular belief, a high-wattage iron will not destroy delicate components. A temperature-controlled soldering iron is designed to switch the heater off when the tip reaches a preset temperature. The powerful heating system only ensures quick thermal recovery during demanding soldering jobs.
3. Closed-Loop Temperature Control Is Important
Having a lot of power under the hood is great, but there’s a reason why rally cars are preferred over semi-trailer trucks when responsiveness is paramount. Soldering is no different. Your soldering station might have 130 watts of heating power, but it isn’t of much use if the tip is allowed to get too cold before the heater kicks in.
Cheap analog soldering irons are bogged down by their slow thermal response time. They can’t react quick enough to compensate for the rapid loss in tip temperature experienced when soldering larger components. This manifests as thermal drift and consequently leads to cold joints.
Good soldering irons get around this problem by incorporating a significantly more agile digital closed-loop temperature control system. This usually involves a heating element, temperature sensor, and a microprocessor control unit.
Related: PS4 Controller Drifting? Here's How to Fix It
Modern soldering stations, and even some cheap soldering irons such as the TS-100 and Pinecil, employ microprocessor-based temperature control, which allows them to react rapidly to maintain precise tip temperature even while soldering high thermal mass components.
Such ability to prevent both temperature undershoot and overshoot is especially important when soldering heat-sensitive integrated circuits.
4. Traditional Versus Direct Heat Soldering Irons
Not all digital soldering irons are built the same. At the outset, the cheaper Hakko FX-888D soldering station might have the same digital microprocessor control logic as the significantly more expensive FX-951, but the latter is light years ahead of it in terms of soldering performance.
The Hakko FX-951 employs a relatively more modern direct heat soldering technology, which not only allows it to react faster to thermal changes, but also maintain tip temperature to a higher degree of precision. And the answer squarely lies in the tip design.
Traditional soldering irons such as the Hakko FX-888D separate the tip from the closed-loop temperature control system. In other words, the tip slides on and off the heating element, and the thermocouple is used to sense tip temperature.
Related: The Best Soldering Irons for Beginners
While this makes it cheaper to replace tips, the actual tip is not only physically further away from the heater and thermocouple, but there’s also an air gap between them. Unfortunately, air is a poor conductor of heat.
The thermocouple is, therefore, unable to record changes to the actual tip temperature with any speed or accuracy. The tip can’t be heated with optimal efficiency, either. This design flaw makes such soldering stations unable to tap into the true potential of their microprocessor-based temperature control system.
Cue modern direct heat soldering stations such as the Hakko FX-951, Pace ADS200, and JBC’s entire product range. The tip in such stations is a composite design incorporating the heating element and thermocouple in a unified package. Not only does this eliminate the air gap, but such design also allows the heating element and thermocouple to be placed right at the proverbial tip.
The ensuing lack of air gap between the tip and the heating element allows such soldering stations to reach operating temperatures in a matter of a few seconds, while also allowing them to respond quickly and eliminate thermal drift. However, the added components and manufacturing complexity makes such tips more expensive to replace.
The Pinecil soldering iron is a good example of this tradeoff. The $25 iron ships without the tip, which ends up costing an additional $15. However, this cheap direct heat soldering iron exhibits a better thermal response than the much more expensive Hakko FX-888D employing traditional tip design.
5. Tip Quality Is the Real Game Changer
The tip geometry of a soldering iron plays a crucial role in achieving controlled, uniform heating of the component leads and pads on the PCB. Cheap soldering irons are usually outfitted with a conical tip since they only have the luxury of including one in the box.
One would assume this would be a general-purpose tip suitable for all types of soldering jobs. In reality, a conical tip is only chosen because it is a geometry that works with SMD soldering. The finer pointed shape of such tips makes it ideal to maneuver around small SMD components—something that would prove impossible with other larger tip shapes.
Unfortunately, the correspondingly smaller contact patch of conical tips cannot achieve the thermal linkage required to bridge the larger pads and leads associated with through-hole soldering. That’s a problem because an overwhelming majority of beginners work with DIY-friendly perforated boards that call for through-hole soldering, which is best served by a chisel tip.
In addition to a limited choice of soldering tip geometries, the anti-corrosive plating found on cheap soldering iron tips is too flimsy to serve its intended purpose. This leads to tips that oxidize within no time, leading to poor thermal conductivity which in turn causes cold joints and burnt components.
A Few Cheap Soldering Irons Get a Pass
The Pinecil and TS-100 are some of the cheaper soldering irons that miraculously fit the criteria of quality soldering irons for a relative pittance. But at their core, they offer the same modern microcontroller-based direct heat tip design as their more expensive counterparts.
Although these irons won’t be as durable or reliable as the pricier alternatives from Hakko, Pace, and JBC, the cheaper irons still offer a terrific value proposition for hobbyists.
About The Author
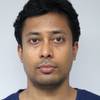
Nachiket Mhatre (8 Articles Published)
Nachiket has covered diverse technology beats ranging from video games and PC hardware to smartphones and DIY over a career spanning 15 years. Some say that his DIY articles serve as an excuse to pass off his 3D printer, custom keyboard, and RC addiction as “business expenses” to the wife.
Subscribe to our newsletter
Join our newsletter for tech tips, reviews, free ebooks, and exclusive deals!
Recommend
-
8
Do I really need to get out the soldering-iron again? 16th July 2018 So I had this idea that it would be nice to listen to music when I get home from work everyday, so I put all my ripped m...
-
16
8 Things To Consider Before Buying Refurbished Devices By Arthur Brown Published 20 hours ago Don't buy a refurbished laptop or s...
-
15
Finance ...
-
5
6 Things to Consider Before Buying a Humidifier By Shan Abdul Published 21 hours ago If you're looking to add a hu...
-
4
7 Things to Consider Before Buying an Air Purifier By Shan Abdul Published 10 hours ago Take a look at our guide o...
-
10
How to Tin a Soldering Iron and Why By Nachiket Mhatre Published 7 hours ago Tinning your soldering iron is...
-
6
4 important tips to consider before buying an electric vehicle
-
7
5 things to always consider before buying a new smartphone
-
7
Hidden Costs To Consider Before Buying A New iPhone
-
4
All About USB-C: Pinecil Soldering Iron ...
About Joyk
Aggregate valuable and interesting links.
Joyk means Joy of geeK