
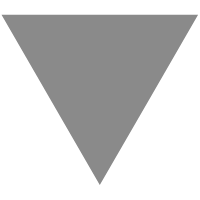
How is Bamboo Lumber Made?
source link: https://www.bambooimport.com/en/how-is-bamboo-lumber-made
Go to the source link to view the article. You can view the picture content, updated content and better typesetting reading experience. If the link is broken, please click the button below to view the snapshot at that time.
How is Bamboo Lumber Made?
Bamboo is a renewable resource that has become one of the most important alternatives to tropical hardwoods in recent years. Upon seeing bamboo flooring, kitchen cabinets or cutting boards you might wonder how round hollow bamboo stems are processed into solid bamboo lumber?
It is important to note that engineered bamboo can be divided into two main groups; "laminated bamboo" and "strand woven bamboo" (or a combination of both). Panels similar to OSB, MDF, particle board, mat boards etc. are also made from bamboo fiber and bamboo chips, but panels made from strips (laminate) or strands (strand woven) are by far the most used in Europe.
Laminated Bamboo
Laminated bamboo plywood is made from flat rectangular bamboo strips that are cut from the bamboo stem. These strips or "slats" are then glued together either horizontally (plain pressed) or vertically (side pressed).
Because laminated bamboo panels consist of individual strips, they show less swelling and shrinkage than solid wood panels. However, the way in which bamboo plywood is constructed does have an influence on its strength, flexibility and stability.
A 1-ply laminated bamboo panel for example, will break easier in its width than a 3-ply or 5-ply panel. A 5-ply panels is also more stable than a 1-ply or 3-ply panel, and is less prone to warping. As a general rule, the more layers, the more stable the bamboo panel.
The number of layers and construction is also important with regard to the appearance of a bamboo panel. Plain pressed bamboo plywood for example has highly visible nodes which results in a very dramatic appearance. The number of layers might be important when using bamboo plywood in applications where the sides are visible, such as stair treads, tables, kitchen tops, cabinets, etc.
1) Bamboo harvest
Moso bamboo (Phyllostachys edulis), is the bamboo species of choice for the production of engineered bamboo panels. This Chinese bamboo is known as the hardest bamboo species in the world and grows on average up to 20 meters tall and 10 cm in diameter.
A bamboo stem reaches its maximum height in just a few months and shall not grow taller or thicker over time. In the following 4 years the fibers will "lignify" and get their extraordinary mechanical properties in terms of hardness, strength, density.
Mature bamboo stems of 4-5 years can be extracted from a bamboo plantation on an annual basis while new shoots emerge from the ground. Bamboo is therefore a very sustainable resource that doesn't need to be re-planted after harvest. This is of course in large contrast to tropical hardwoods that often require 50-100 years to reach maturity.
2) Selecting bamboo poles
Bamboo poles with an average diameter of 9 cm are selected for the production of engineered bamboo products. These are cut into lengths of 250 cm.
3) Splitting bamboo poles
The bamboo poles are placed in a special machine which converts them into rough bamboo slats. The poles are pushed through a metal "splitter" (knives in star shape) until the entire stem is cut into slats.
4) Planing bamboo slats
The bamboo slats are initially still very irregular in shape and structure. To eliminate their green outer layer and internal nodes, the slats are planed in the dimensions 22 x 6 mm.
5) Boiling bamboo slats
To protect bamboo from future insects attacks or fungi, the slats are boiled in hydrogen peroxide for ± 7 hours. This treatment has the added advantage that it bleaches the strips which results in a uniform natural color.
6) Carbonizing
Optionally, bamboo strips are carbonized in a high-pressure tank for several hours. The combination of heat and pressure releases natural starch in bamboo strips which gives it a typical brown caramel color.
7) Drying and sanding
After the boiling / carbonizing treatment, bamboo strips are dried in a kiln for about 5 days until they reach a moisture content of approximately 8-10%. Once dry, the bamboo strips are sanded to their final 20 x 5 mm dimensions.
8) Quality control bamboo strips
After the bamboo strips have been treated, dried and sanded they are checked one last time on color and quality before being processed into panels.
9) Plain pressed
As mentioned earlier, bamboo strips can be glued together either horizontally or vertically. In a "plain pressed" panel the bamboo strips are pressed together facing up. This results in a 1-ply where the pattern and characteristic of the bamboo nodes are clearly visible.
Plain pressed bamboo plywood has a thickness of 5 mm. In order to make thicker panels different layers are glued together (usually crosswise).
10) Side pressed
In a "side pressed" panel the bamboo strips are pressed together vertically. This results in a 1-ply where the pattern and characteristic of the bamboo nodes are not clearly visible.
Side pressed bamboo plywood has a thickness of 20 mm. In order to make thicker panels or beams, several layers are glued together.
11) Cutting to size
A band saw is used to convert 20 mm side pressed plywood into thinner panels. This way the individual sheets can be used to build 3-5-7 or 9-ply bamboo panels.
12) Sanding
Sanding is the final step in the production process to accomplish a perfectly flat a smooth surface.
13) Quality control
All bamboo panels are checked on last time for production flaws during packaging.
Strand Woven Bamboo
For strand woven bamboo largely the same steps apply as with laminated bamboo except that the strips are not glued together horizontally or vertically. Instead, raw bamboo strands are used which are compressed under high pressure to create a new "composite" material.
The density of strand woven bamboo is much higher than laminated bamboo with 1200 kg / m3 instead of 700 kg / m3. This makes strand woven bamboo also a lot harder than laminated bamboo with a Janka hardness of 2800 lbf instead of 1380 lbf.
The appearance of strand woven bamboo is completely different from bamboo plywood. Strand woven bamboo looks similar to wood with its flamed structure and bamboo nodes that became virtually invisible.
1) From strips to strands
After boiling or carbonizing the bamboo strips as previously described in step 5-6, the strips are crushed into rough fibrous bamboo strands.
2) Impregnating bamboo strands
The bamboo strands are impregnated with glue before putting them in the press.
3) Compressing
The bamboo strands are placed in a massive industrial press and compressed with a pressure of 2,500 tons.
4) Cutting to size
Strand woven bamboo panels are available in a maximum thickness of 20 mm, otherwise they would become too heavy. 30-40 mm thick panels are sawn into smaller boards of max 10-30 cm wide. These bamboo planks can then be processed into bamboo flooring, decking or siding.
Also interested to work with engineered bamboo? Order your bamboo panels today in our online shop!
Recommend
About Joyk
Aggregate valuable and interesting links.
Joyk means Joy of geeK