
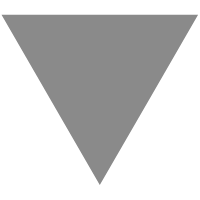
TI Hopes to Extend EV Drive Time With New DC-DC Bias Supply Module
source link: https://www.allaboutcircuits.com/news/texas-instruments-new-dc-dc-bias-supply-module-for-evs/
Go to the source link to view the article. You can view the picture content, updated content and better typesetting reading experience. If the link is broken, please click the button below to view the snapshot at that time.
News
TI Hopes to Extend EV Drive Time With New DC-DC Bias Supply Module
4 days ago by Jake Hertz
The powertrain is the heftiest part of an EV. To target this component-heavy system in EVs, TI says it is targeting distributed power architectures for more integrated gate driver circuitry.
While EVs are undoubtedly gaining traction, they still face significant challenges—like cost, performance, and range. Historically, engineers have tried to address these concerns by optimizing EV batteries. Now, however, Texas Instruments is turning its attention to optimizing the powertrain, the heaviest part of an EV.

An example of an EV powertrain. Image used courtesy of EVreporter
Today, TI announced a new isolated DC/DC bias-supply module meant to cut down the area and cost of EV powertrains. This device is said to slash typical power solution volumes by 50 percent in high-voltage applications ranging from EVs and hybrid EVs to motor-drive systems and grid-tied inverters.
All About Circuits had the chance to sit down with Ryan Manack and Steve Lambouses from TI to hear more about the product firsthand.
A Distributed Power Architecture for Powertrains
As its name suggests, the powertrain is the part of an EV that is responsible for delivering power to the vehicle. The major components in an EV powertrain tend to be the battery itself, the battery management system, the onboard charger, AC/DC conversion circuitry, and DC/DC conversion circuitry.
At a system level, the three major semiconductor components for powertrain systems are the MCU, isolated gate drivers, and power semiconductors. With an increasing need for reliability, diagnostics, and safety compliance, isolated gate drivers have recently become a primary component of focus for EV designers.
Usually, powertrain systems leverage one big isolated DC/DC power supply to power all of the gate drivers, but this requires bulky external circuitry.

The distributed architecture has each gate driver with its own bias supply. Image used courtesy of Texas Instruments
A more size- and power-optimal solution, in Texas Instruments’ opinion, is a distributed power architecture for isolated gate driver circuitry. In this scheme, every isolated gate driver has a smaller, more heavily integrated dedicated bias supply.
"In legacy systems, you could use one transformer to bias all of these gate drivers, but in automotive systems, where redundancy is key, and small size and weight is key, we see more customers moving toward something called a distributed power architecture," explains Ryan Manack, TI's director of automotive systems engineering marketing.
"TI has spent time thinking, 'What do we do to optimize this architecture?' How do we reduce the design cycle time, the component count, the size and weight to help customers extract the full performance of these traction inverter systems or these on-board charger systems?"
By increasing integration in a smaller transformer module, TI says designers can significantly decrease the BOM for the powertrain on a system level.
TI Doubles Down on Integration
In an effort toward this distributed architecture, TI today announced its UCC14240-Q1, a high-isolation voltage DC/DC module. "We wanted to simplify design for design engineers to make the integration easier and to reduce the number of electronic boxes that go inside the automobile," Manack said.

Functional block diagram of the UCC14240-QI. Image used courtesy of Texas Instruments
Designed to provide power to isolated IGBT or SiC gate drivers, the new module integrates a transformer, a DC/DC controller, and on-chip protection—including under-voltage lockout and over-temperature shutdown. According to the datasheet, the device can achieve:
- Switching frequencies up to 17MHz
- CMTI performance of more than 150 V/ns
- Isolated output power of > 1.5 W (typical) at ~55 percent efficiency

Using the UCC14240-Q1, engineers can purportedly reduce volume by up to 75 percent. Image used courtesy of Texas Instruments
By integrating some of the larger components into one IC, TI’s UCC14240-Q1 helps designers save significant area and cost in their powertrain designs. According to TI, the device allows for a 75 percent decrease in volume and a BOM decrease of more than 15 components.
Steve Lambouses, TI's VP and general manager of high-voltage power, explains that legacy solutions with large transformers operate at frequencies below the AM band (550 kHz or below) and have creepage and clearance safety specifications to abide by.
"Conversely, with the UCC14240-Q1, the transformer is physically integrated inside the package," Lambouses notes. "We're switching at a much higher frequency. The height alone is shrunk by over 7 mm (at 3.55 mm) from the traditional 11 mm. And, where traditional solutions are at 2,000 V RMS, we're up to 3,000 V RMS in a smaller package."
Addressing Range Anxiety
Range anxiety is one of the prevailing drawbacks to EV adoption.
To address this limitation, TI designed the UCC14240-Q1 with 60 percent efficiency (double the efficiency of competing bias supplies), which effectively extends a vehicle's driving distance between charges. This dual-output power device measures 3.55 mm high, allowing engineers to cut a designer's power solution volume in half. This compact size also enables the module to be placed on either side of the PCB.
The UCC14240-Q1's integrated closed-loop control allows for precise accuracy (±1.0%) in ambient temperatures ranging from -40°C to 150°C. This makes the new module useful for driving IGBTs, SiC, and GaN switches at high frequencies. Tapping into TI's integrated transformer technology, the device offers 3.5-pF primary-to-secondary capacitance. This feature also side steps the EMI offset by high switching speeds.

Diagram of a distributed power architecture in an EV traction inverter, including TI's UCC14240-Q1. Image used courtesy of Texas Instruments
"It's no surprise that the industry is going toward higher voltages and lower corresponding currents. The UCC14240-Q1 offers support for 400 V and 800 V systems, and the voltage rating for the device is 3,000 V RMS," Lambouses explains. "Regardless of where the market goes from a market perspective, we've got it covered with ultimate flexibility."
Recommend
About Joyk
Aggregate valuable and interesting links.
Joyk means Joy of geeK