
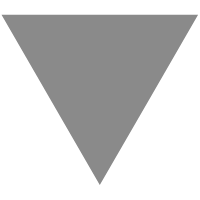
Predictive Analytics: The Future For The Chemical Industry | Codecondo
source link: https://codecondo.com/predictive-analytics-the-future-for-the-chemical-industry/
Go to the source link to view the article. You can view the picture content, updated content and better typesetting reading experience. If the link is broken, please click the button below to view the snapshot at that time.
Why Predictive Analytics, Not Descriptive Analytics, Is The Future For The Chemical Industry?
Chemicals are the backbone of many end-market industries, from pharmaceuticals to automotive production. If chemical plants aren’t able to meet supply and quality demands, all these other industries suffer.
The pressure on chemical plant managers to improves production quality and consistency, increase plant safety, and reducing product costs is high. They need all the tools at their disposal to run a resilient plant with minimum downtime and high operating efficiency.
Advanced analytics is a still-evolving field that offers an enormous amount of assistance to plant managers by cutting downtime, costs, and safety incidents. As analytics capabilities develop, it’s clear that predictive analytics, not descriptive analytics, is the future for the chemicals industry.
What is the difference between descriptive and predictive analytics?
For several years, descriptive analytics, or business intelligence (BI), is the most widely-used type of analytics for various verticals. It involves gathering and interpreting historical data to understand past events, and produces simple data visualizations that help users to quickly grasp the implications of the data. It’s relevant for use cases like recording profit and loss, monitoring marketing campaigns, and tracking sales levels.
Descriptive analytics has the advantage of being easy to use and quick to apply. Today, most BI tools offer automation and intuitive dashboards that make them even more user-friendly. Most employees can implement BI tools and gain value from their insights with little to no training. Chemical plants use descriptive analytics to track product quality incidents and part failures and to verify they are meeting KPIs and progressing towards their goals. But BI tools don’t dig deep into data insights, and can’t make predictions.
In contrast, predictive analytics applies artificial intelligence (AI) and machine learning (ML) to crunch the mass of big data generated by IIoT devices and sensors to recognize emerging patterns and predict likely outcomes. In the last few years, predictive analytics adoption has increased, enabling chemical process companies to forecast trends in order to prepare for risk, opportunity, and/or changes that are still some way down the road.
Predictive analytics is a broad term that includes many applications, such as sentiment analysis, demand forecasting, predictive modeling, predictive maintenance, predictive monitoring, and root cause analysis. Chemical plants use predictive maintenance tools, for example, to generate early alerts about anomalies that indicate impending part failure, so that maintenance teams can repair parts before they fail. Predictive monitoring enables chemical plants to move beyond a focus on parts alone to identify inefficiencies or bottlenecks anywhere in the process, while root cause analysis helps plant engineers to understand the causes of equipment or process issues.
Predictive analytics is already helping plant managers to run a more efficient plant that drives value. Duane Dickson, Global and US Chemicals sector leader at Deloitte, writes that “these technologies are now advanced enough that they can integrate with chemicals companies’ core conversion and marketing processes to digitally transform operations and enable ‘smart’ supply chains and factories as well as new business models.”
How does predictive analytics help the chemical industry?
Maintain high quality
If product quality drops, millions of end products will have to be recalled. Equally, inefficiencies can delay millions of crucial end products from reaching the market. Today’s COVID-19 vaccines, for example, involve a number of base chemicals produced by different factories, and if one of those components is delayed or quality is compromised, the entire vaccine supply chain fails. Product recall is becoming more frequent as quality regulations rise, and often hits the headlines, affecting both your and your customers’ reputations.
Consistent quality can only be maintained when you constantly monitor a plant for anomalies and pick up on them early enough to prevent them from significantly affecting product quality. With predictive monitoring and predictive maintenance, plants can spot early signs of bottlenecks and equipment failure which can lower the quality of the product, thus correcting quality inconsistencies before they become serious and preventing a low-quality batch from ever leaving your plant.
Chemical plants also have to grapple with rapid fluctuations in the volume of their orders, which make it difficult to ensure consistent product quality. They need full supply chain visibility to quickly ramp up or scale down raw material orders in accordance with customer demand. Predictive analytics helps open up full visibility into complex supply chains that frequently span continents and suppliers, as well as assisting companies to forecast customer demand so they can be prepared for changes in customer orders.
Ensure safety
Chemical plants handle many hazardous chemicals that can cause serious environmental damage and risk to human health and are subject to numerous safety regulations from health, safety, and environmental bodies. In America, fines for non-compliance begin at $12,600 per violation, climbing up to $127,000, but the damage to your reputation from harmful accidents can be incalculable.
Predictive analytics reduces the need for manual equipment and process checks, which can be hazardous to employees. Additionally, by spotting early signs of anomalies, predictive analytics solutions help reduce the risk of leakages, spillages, flares, and other incidents which can harm the environment, your employees, and/or nearby residents. For example, predictive analytics software in one chemical plant identified an anomaly in the measured level of sulphuric acid in a tank. Investigation revealed that the tank level sensor had stopped working, so there was no reliable information about acid levels. Once the process engineer learned about the sensor failure, they sent an employee to manually check tank levels at regular intervals, until the next scheduled shutdown allowed them to fix the sensor. Without this alert, the tank could have been overfilled and caused a hazardous spill.
Reduce costs
Keeping costs down has always been important for chemical plants, but a recent rise in customized, small-batch orders has made it even more imperative. Small-batch orders add to the difficulties of delivering low-cost, high-quality products on time since plants lose their ability to leverage economies of scale.
Predictive analytics can help reduce costs in direct and indirect ways. For example, predictive alerts can enable maintenance teams to repair a part rather than replace it, thereby extending equipment lifetime and cutting equipment costs. Additionally, predictive maintenance solutions may notice issues with a small part that is inexpensive and quick to replace, but if the issue continued undetected, it could have damaged equipment that would have been costly and required extended, unplanned downtime to deal with.
Predictive monitoring also helps cut energy use and raw materials waste. An efficient plant needs less energy and doesn’t waste resources on manufacturing poor-quality end products. Energy can make up half the costs of chemical processing. Additionally, reducing product recalls and unplanned downtime makes your plant more reliable, boosting your reputation among customers who will choose a chemical manufacturer that they can trust to deliver quality products on time.
Predictive analytics offers value for the chemical industry
Predictive analytics solutions are already delivering value for a number of use cases, enabling chemical plants to cut costs, reduce waste, improve product quality, and increase plant safety. As the chemical industry continues to respond to changes in supply patterns and customer demand following the crisis of COVID-19, predictive analytics will become even more important to drive growth, reliability, and profitability in the chemical manufacturing industry.
Originally written by Chen Linchevski, CEO, Precognize.
Also Read: Promising Augmented Analytics- Why Advanced Business Analytics Is About AI-Based Approaches?
Recommend
About Joyk
Aggregate valuable and interesting links.
Joyk means Joy of geeK