
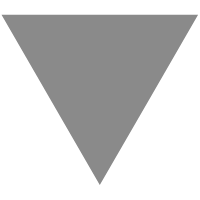
3D printing boats is becoming standard practice
source link: https://www.3dprintingmedia.network/3d-printing-boats-is-becoming-standard-practice/
Go to the source link to view the article. You can view the picture content, updated content and better typesetting reading experience. If the link is broken, please click the button below to view the snapshot at that time.
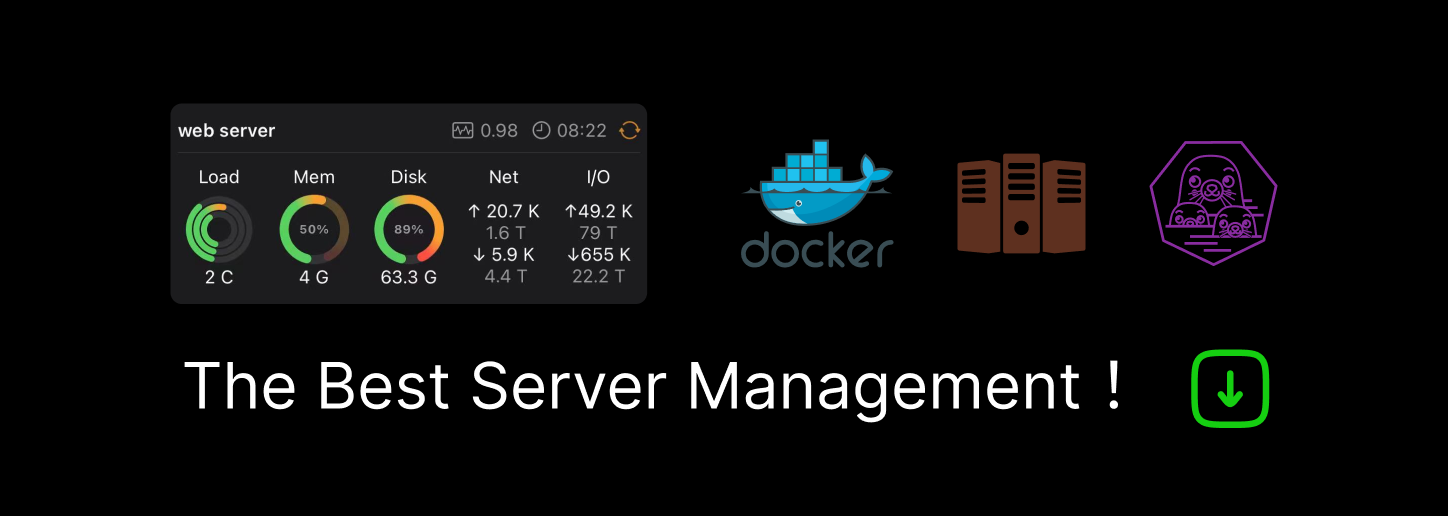
3D printing boats is becoming standard practice
Latest successful demonstration by RISE institute in Sweden shows a solid trend
Davide SherDecember 19, 2020
A new project just published by Emil Johansson, Research Scientist Additive Manufacturing at RISE Research Institutes of Sweden, demonstrated a functional fully 3D printed boat (shown in the video above). This is the latest of a long string of projects that has shown how new large-format extrusion systems—either based on cartesian or multi-axis robotic architectures—are making the process of 3D printing boats a fairly standardized (or, at least, standardizable) practice.
In this application case, the researchers tested a 3D printed motorboat on the Swedish west coast in the middle of December, while live-streaming the event. The 3D printed boat handled the water perfectly. “This is the pinnacle of a remarkable collaborative effort,” Johansson said. “Printing a boat is something my colleagues Lenny Tönnäng, Jan Johansson and I at RISE Research Institutes of Sweden have dreamt of for many years. Together with an innovative team at Cipax and Pioner boats, led by Dag Eirik Thomassen and Lars Haugli, we decided to make it happen.”
In this case, the boat itself was 3D printed in one piece using industrial robot based additive manufacturing, a technology that the researchers have been working on with Anders Spaak at ABB for several years. The work part of the research project DiLAM, funded by Vinnova, the Swedish Energy Agency and Formas through the strategic innovation program Produktion2030.
This is the latest in a long string of projects that began a few years ago, when the entire marine and maritime industries finally began to open up to AM technologies beyond some basic prototyping.

From prototypes to 3D printing boats
In the beginning, it was Livrea Yacht, an Italian studio that was probably the first to envision the idea of 3D printing an entire boat, based on the experience of using AM for prototyping new yacht designs. Livrea founded the startup Ocore to develop a robotic extrusion technology capable to 3D print an entire sailboat hull in Sicily, with support from LEHVOSS and Autodesk.
Their success in 3D printing the entire sailboat hull in late 2018 was somewhat overshadowed by an even more impressive project that was completed just a few weeks before in the US, by the University of Maine and ORNL. Using Ingersoll’s massive 3D printer, the well-funded American institutions created the world’s largest entire 3D printed boat, which now holds a total of 3 Guinness World Records. This time the boat was 3D printed using a large cartesian extrusion system, using a carbon fiber reinforced nylon composite pelletized material.
Then came MAMBO, the first full and fully functional 3D printed boat using continuous fiber composite materials, this time, again, developed by another Italian startup called moi Composites. In this case, the boat, developed and designed in collaboration with Autodesk, was produced using multi-axis robotic extrusion of a continuous fiberglass composite thermoset material.
While the continuous fiber extrusion process may still be a bit farther away in terms of achieving the necessary cost-efficiency and speed, chopped fiber composite extrusion systems have now been shown to be more than effective in printing very large structures, such as boat hulls, in a single run. This is a gigantic achievement and it now seems pretty clear that this will become a more widely adopted technology in the boat manufacturing industry in the years to come.

The ability to build a one-off product such as a boat or small yacht, directly from CAD, without having to build expensive and time-consuming molds, that are only used once, can bring immediate and clear benefits. On the other hand, large format 3D printing technologies can bring benefits to marine and maritime mold-manufacturing as well.
Another large format cartesian 3D printing manufacturer, Thermwood, has demonstrated this by 3D printing several sections from a 51-foot long yacht hull mold to show how a single hull mold may be sufficient to manufacture even larger vessels, such as yachts. The printed sections of the test mold were made of carbon fiber reinforced ABS from Techmer PM. In this case, ABS was chosen because of its physical properties and relatively low cost compared to other reinforced thermoplastics.
From 3D printing boats to spare parts
If 3D printing boats—intended as small, full size, entire boats—is among the most fascinating applications of 3D printing, one of the most valuable applications of AM in the maritime industry is on-demand production of spare parts. This is now rapidly becoming a very valuable and high-potential business segment for some very large operators in the maritime industry.
Large format metal 3D printing companies such as AML3D and MX3D have published some of the first application cases for metal 3D printed maritime spare parts. Both technologies are based on a WAAM process and are able to produce very large metal parts with very high metal deposition rates. Other initiatives saw Singapore-based firm Tytus3D also contribute its own metal 3D printing technology to develop maritime applications, in a joint industry project collaboration with segment operators. In Australia, local firm SPEE3D made its kinetic consolidation (cold blown powder) metal 3D printing technology available to produce spare parts for the Australian Navy.

This is only the tip of the iceberg (although “iceberg” may not be the best metaphor to use in this context). Some very large firms active in the maritime industry, such as Wilhelmsen, thyssenkrupp, Yinson, Wärtsila, Kawasaki Heavy Industries, along with large consultancy groups such as DNV GL, are making significant investments into developing the infrastructure to produce boat spare parts by AM, benefiting from on-demand and digital warehouse capabilities.
In a segment such as the maritime industry, where ships can have a lifespan of several decades, storing many different types of very large spare parts presents significant economic challenges. In particular, Thyssenkrupp and Wilhelmsen are collaborating on leveraging thyssenkrupp’s deep expertise in AM alongside Wilhelmsen’s in-depth maritime expertise and direct ongoing experience in understanding the needs of vessel fleet managers, to provide on-demand AM production services to large maritime industry operators.
Norway-based DNV GL issued a certificate making thyssenkrupp’s TechCenter Additive Manufacturing the world’s first producer of 3D printed parts for maritime applications to receive manufacturer approval from DNV GL. As an approved supplier for maritime and general industrial 3D printed components, thyssenkrupp aims to continue to integrate additive manufacturing in its maritime business.
Back to stunning 3D printed scale models
Maritime industry operators that have been gradually introducing 3D printing in their process for spare parts production or yacht design and development have also started to identify another valuable application of 3D printing in the production of beautiful and highly detailed scale models. Italian firm Meg Industry is one of these firms and discussed this part of their work in an interview with 3dpbm’s Italian language portal Replicatore.

Recommend
-
7
Want more videos like this? Every day we send an email with the top videos from Digg. It's likely not lens distortion that caused the curious appearance. Instead, it's some...
-
8
Candela’s P-12 electric hydrofoil water taxi unveiled, costs 85% less than gas boats to runPublic transportation just got way cooler. Premium Swedish electric boat maker Candela has just unveiled the new Candela P-12, an electric hydrofoil wa...
-
14
June 3, 2021 ...
-
4
News The Story of Bluetooth: The Slow Road to Becoming an Industry Standard 3 days ago by Lianne Frith Bluetooth seems like a...
-
12
Who Flew Across The Atlantic First? The Airborne Boats Of 1919 Aviation history is a bit strange. People tend to remember some firsts but not others and — sometimes — not even firsts. For exam...
-
11
Ram Bandla April 24, 2022 3 minute read
-
6
Rebekah Vardy denies it was standard practice to leak storiesBy Paul GlynnBBC News, at the High CourtPublished21 minutes ago
-
6
My review of the C standard library in practice February 11, 2023 This article was discussed
-
8
Tesla technology inches closer to becoming industry standard as Rivian joins its charging network by Tom Krisher...
-
9
Tesla's EV plug is closer to becoming the industry standard following a move by an automotive group by Tom Krisher...
About Joyk
Aggregate valuable and interesting links.
Joyk means Joy of geeK