
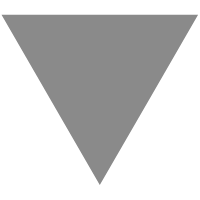
For GM auto union workers, there's still a lot to learn about EVs
source link: https://www.cnbc.com/2022/10/16/how-one-gm-auto-plants-union-workforce-is-learning-to-make-evs.html
Go to the source link to view the article. You can view the picture content, updated content and better typesetting reading experience. If the link is broken, please click the button below to view the snapshot at that time.
For GM auto union workers, there's still a lot to learn about EVs
In this article
In 2015, Marland “Lanny” Brown learned how to build an all-electric car.
A member of United Auto Workers Local 5960, he’d been an hourly employee for General Motors for nearly 31 years, mostly at its vehicle assembly plant in Lake Orion, Michigan, when he joined a core team of 15 fellow Local 5960 workers sent to GM’s technical center in Incheon, South Korea, for training to assemble the Chevrolet Bolt EV.
The Orion plant, in operation since 1983, was beginning to transition from making a variety of internal combustion engine (ICE) vehicles to EVs. Following their reskilling, the popular term for upgrading job skills, Brown and the team went back to Orion and over several months trained roughly 1,000 other assembly workers on both the subtle and the substantial differences in putting together an EV. Part of the changes for workers’ duties were related to retooling in the body shop and on the engine line to accommodate components and production processes distinct to EVs.
While much of the EV assembly, Brown said, is similar to an ICE vehicle’s — such as installing doors, windows, tires, brakes, seats and instrument panels — the powertrain, comprising the engine and transmission, are remarkably different. In place of a gas-powered engine and multi-speed transmission is a lithium-ion battery pack, mounted underneath the cockpit, which energizes a zero-emissions electric motor and single-speed transmission. “Going down the engine line, instead of putting on a carburetor, we’re putting on a power distribution unit,” Brown said, citing one example.
The first Bolts started rolling down the line in October 2016, marking GM’s initial foray into an all-electric vehicle (the discontinued Chevy Volt was a plug-in hybrid), and well before the automaker announced in 2021 that it would make only EVs by 2035. Yet for the next three years, the Orion plant also continued building two ICE vehicles — the Chevy Sonic and Buick Verano — before switching over exclusively to the Bolt in 2020 and then adding the Bolt EUV (electric utility vehicle) in 2021.
In the industry, this is called a slow build, said Jack Hund, the launch manager at Orion, who’s overseen numerous new model introductions at various GM plants during his 23 years with the company. “We started slowly introducing the Bolt on the assembly line,” he said, a process that can take up to a year while working out the bugs. “We know it’s not going to be smooth the first time.”
“Progressively, we built more and more [EV] units,” Hund said. “The people on the line were so used to the ICE vehicles, it took a little time for them to wrap their arms and minds around it. There was a different skill set they had to apply to the EV,” for instance, learning the nuances of new torque tools to fasten parts onto the car with a specific amount of pressure.
“Being in an ICE environment my entire career, the big change has to do with high-voltage electrical cable connections,” Brown said. There’s specialized training required for all the assembly workers on how to deal with those potentially dangerous connections in a safe manner, he said. In essence, “it takes more of an electrician than it does a mechanic” to assemble an EV, Brown said..
Besides on-the-job reskilling, GM provides some workers with a virtual component. “We have a system where you’re on a computer and doing the elements of the work in [a prescribed] order,” said Reuben Jones, the plant manager at Orion. “They get mental reps to help them once they get to the line. Building vehicles at the right quality level and in a safe manner is extremely important. Virtual training has taken things to another level. That saves time, that saves money and helps us get the product to market much faster.”
Another off-site training program takes place at GM’s Technical Learning University (TCU) in nearby Warren, Michigan. The recently upgraded center houses manufacturing laboratory facilities that simulate steps along the assembly line, including robotics and sheet metal fabrication. In addition to that technical training, “We intertwine what we’re now calling human skills, which incorporate how to listen, how to have teamwork and critical-thinking skills,” said Kimberlea Dungy, global technology learning lead at TCU.
As the reskilling of UAW workers continues during the Big Three automakers’ steady migration to EVs, there’s a related issue that concerns the union. Because there are fewer parts in EVs than in ICE vehicles, Volkswagen Group’s then-CEO Herbert Diess said in 2019, building an EV requires about 30% less effort, which means cutting jobs. While that figure has been repeated by other executives and researchers, there has been no empirical study to support the assertion. For its part, the UAW continues to study the matter and remains vigilant.
The UAW’s current contracts with GM, Ford and Stellantis (formerly Fiat Chrysler), ratified in September 2019, help protect workers at assembly plants like Orion that switch from ICE to EV production. Essentially, the UAW and each of the companies negotiate to bring massive EV-related investments into current UAW-represented facilities to preserve jobs at those locations and offer reskilling opportunities.
In a September interview with the Washington Post, GM CEO Mary Barra addressed the issue of EV-related jobs, stating that “we’re allocating EVs or components for EVs into our existing footprint. So that’s something we’ll continue to do. It’s an advantage not only because of the workforce, it’s also an advantage because we have the facility.”
“Historically, there’s always been anxiety around the loss of jobs, but since EVs have found their way into the Big Three [assembly plants], we’re understanding more about them,” said David Michael, communications coordinator for UAW Local 5960. No jobs have been lost at Orion as a result of EV production, he said, and in fact, “we see the addition of jobs.”
When asked about the fate of workers whose jobs were specific to ICE vehicles and are no longer needed, Michael said they “are now either building EV components, drivetrains or doing alternative work to build EVs. They’re all right here. We had an assembly line where [ICE] engines came down, and now they’re electric drivetrains.”
The likelihood of continued job retention and hiring at Orion is promising following the announcement earlier this month that GM will increase Bolt production from nearly 44,000 vehicles this year to more than 70,000 in 2023. While the overall U.S. market for EVs is still only around 5% of new-car sales — but rapidly growing — among the 1.65 million EVs that were sold in the first nine months of 2022, the Bolt accounted for more than 22,000.
Recommend
About Joyk
Aggregate valuable and interesting links.
Joyk means Joy of geeK